Rowsum Services
China's Top PCB Manufacturing Industry Supplier
We don’t just manufacture PCBs, we engineer success for your business.
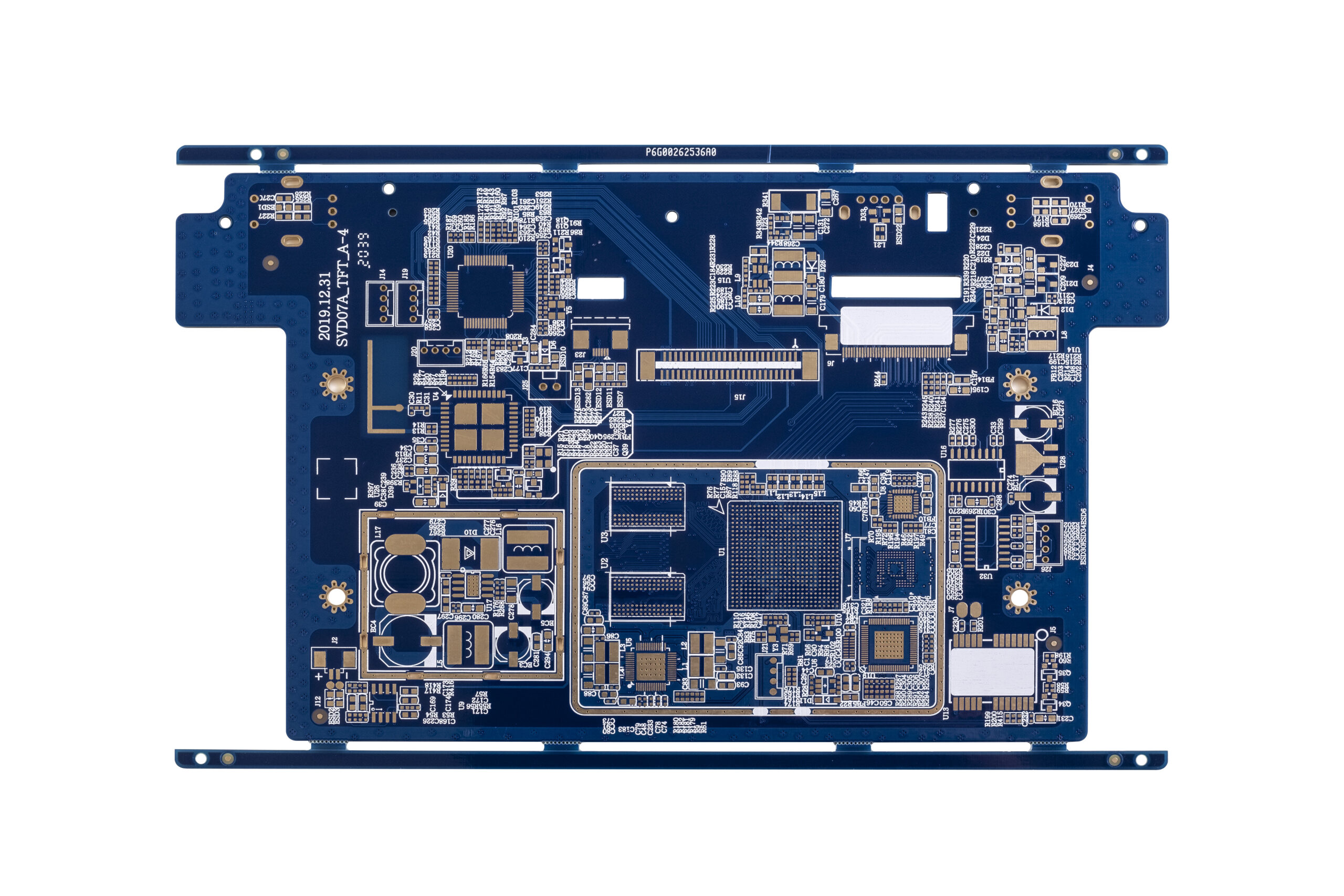
Empower Your Innovation with Our PCB Manufacturing Services
Experience the power of over four decades of expertise in the complex world of PCB manufacturing with Rowsum. Our services are tailored to meet the diverse needs of businesses across various industries. Whether you’re in need of single-sided, double-sided, or multi-layer PCBs, we’re equipped to deliver high-quality products crafted to your specifications. With our commitment to quality, efficiency, and innovation, we’re not just a service provider – we’re a trusted partner in your business’s journey to success.
- Our Commitment to Quality: Advanced Manufacturing Equipment and Strict Processes
- Unbeatable Lead Times: Our 50,000 Square Meter Monthly Production Capacity
- No Minimum Order Requirements: We Accommodate Orders of Any Size
- Competitive Pricing: Direct Factory Pricing Without Middlemen Markup
- Dedicated Project Manager for Seamless Communication and Support
- Fastest Sample Production Time: As Quick as 24 Hours
Navigating Your Path to Success with Rowsum's PCB Services
Explore our comprehensive guide to understand how our PCB solutions can empower your business.
Where Are Our PCB Used? Exploring Diverse Applications
From everyday electronics to advanced medical devices, our high-quality PCBs are empowering innovation across a wide spectrum of industries. Discover how our PCBs are integral to the technologies shaping our world.
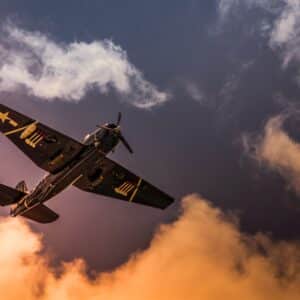
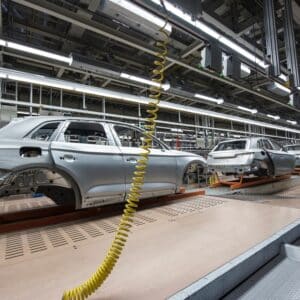
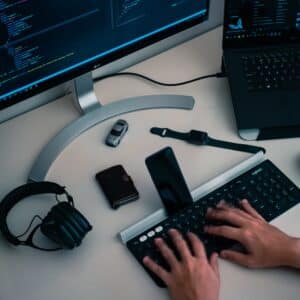
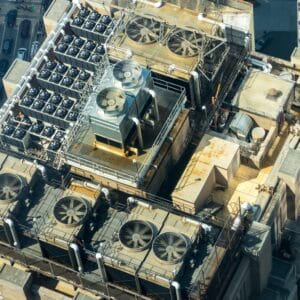
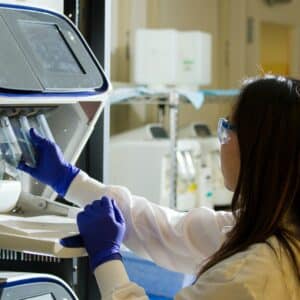
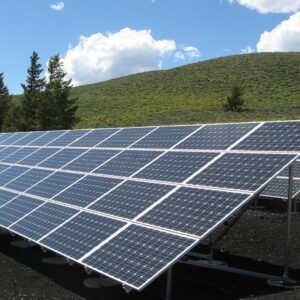
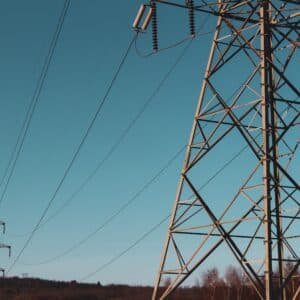
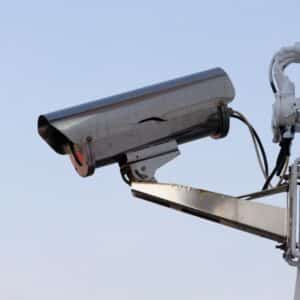
Choosing the Right PCB A Guide to Our PCB Types
Understand the unique features and benefits of each PCB type to make an informed choice for your specific needs.
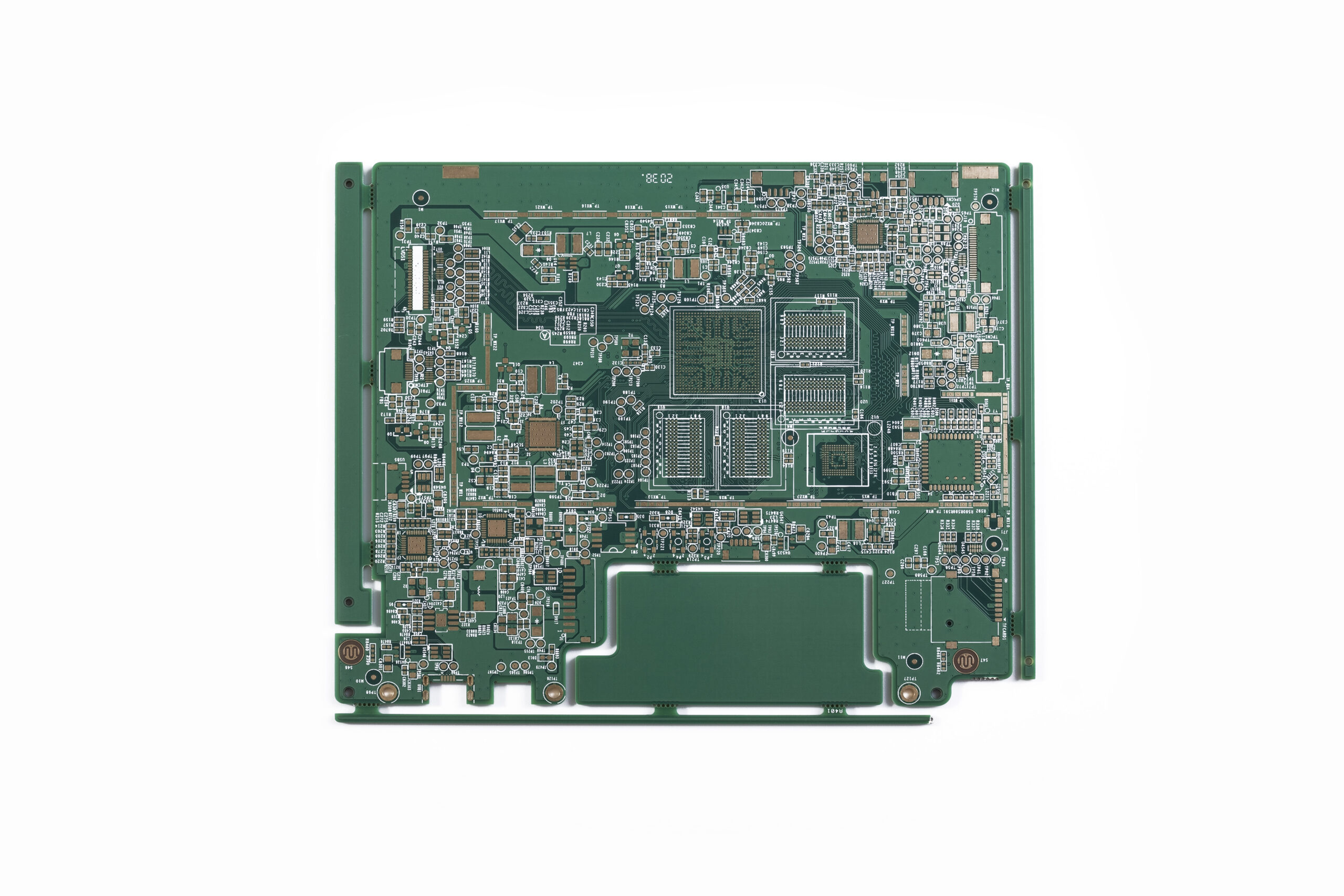
Rigid PCBs: Your Comprehensive Guide
A Rigid PCB is a type of Printed Circuit Board that uses a solid, inflexible substrate material, providing a rigid structure that holds the electronic components in place. They are the most common type of PCBs due to their durability and ease of use.
Rigid PCBs can be made from a variety of materials, each suited to different applications:
FR-4: The most common material, known for its good heat resistance and electrical insulation properties.
Polyimide: Used for high-temperature applications, it’s flexible and chemically resistant.
Aluminum: Known for excellent heat dissipation, it’s commonly used in LED lighting and power converter applications.
Rogers: A high-frequency laminate material ideal for applications where signal integrity is crucial.
Ceramic: Offers excellent thermal conductivity and high-temperature stability, often used in high-power applications and aerospace industry.
PTFE (Teflon): Used for high-frequency applications due to its low dielectric constant and low loss tangent.
CEM (Composite Epoxy Material): A less expensive alternative to FR-4, used in a variety of applications.
High-TG FR-4: A variant of FR-4 with a higher glass transition temperature, used where high heat resistance is required.
The choice of material will depend on the specific requirements of your PCB design, including factors like operating frequency, thermal considerations, rigidity, and cost.
- Single-Sided Rigid PCB
– Definition: Single-sided rigid PCBs have all electrical components and circuits on one side of the board.
– Applications: Ideal for simple devices like calculators, printers, and radios.
– Choosing Single-Sided PCB: If your circuit design is simple and cost is a concern, single-sided PCBs are a good choice.
- Double-Sided Rigid PCB
– Definition: Double-sided rigid PCBs have circuits and components on both sides of the board.
– Applications: Used in more complex devices like power supplies, automotive dashboards, and HVAC systems.
– Choosing Double-Sided PCB: If your circuit design is more complex and requires components on both sides, double-sided PCBs are a suitable choice.
- Multi-Layer Rigid PCB
– Definition: Multi-layer rigid PCBs consist of three or more conductive layers of circuits, with insulation between each layer.
– Applications: Used in highly complex and dense circuit applications like computers, satellites, and data storage devices.
– Choosing Multi-Layer PCB: If your circuit design is highly complex and requires multiple layers of components, multi-layer PCBs are the best choice.
Advantages
– Durability: Rigid PCBs are highly durable and can withstand harsh conditions.
– Cost-effective: They are generally less expensive to produce than other types of PCBs.
– Ease of assembly: Rigid PCBs are easier to assemble and install than flexible PCBs.
Disadvantages
– Lack of flexibility: Rigid PCBs cannot be bent or folded, which can limit their use in certain applications.
– Size: Because they cannot be bent or folded, rigid PCBs can take up more space than flexible PCBs.
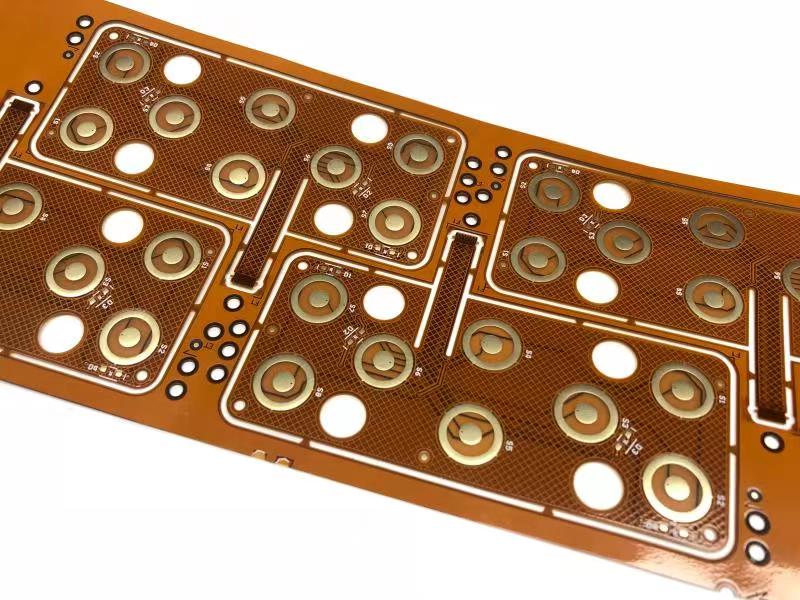
Flexible PCBs: Versatility at Your Fingertips
Flexible PCBs, as the name suggests, are flexible and can be bent or folded to fit into small or unconventional spaces. This makes them ideal for applications where space is at a premium or where the PCB needs to conform to a specific shape.
– Flexibility: The primary advantage of flexible PCBs is their ability to be bent, folded, or flexed while maintaining circuit integrity. This allows for more compact and creative designs.
– Lightweight and Thin: Flexible PCBs are typically lighter and thinner than rigid PCBs, which can be beneficial in applications where weight and space are critical factors.
– Durability: Despite their flexibility, these PCBs are highly durable and can withstand harsh conditions, making them suitable for challenging applications such as aerospace and medical devices.
Flexible PCBs are typically made from materials like Polyimide, Polyester, and PTFE (Teflon), which offer flexibility and good heat resistance.
Advantages
– Flexibility: As their name suggests, flexible PCBs can be bent, folded, or flexed, allowing for more compact and creative designs.
– Lightweight and Thin: They are typically lighter and thinner than rigid PCBs, which can be beneficial in applications where weight and space are critical factors.
– Durability: Despite their flexibility, these PCBs are highly durable and can withstand harsh conditions.
Disadvantages
– Cost: Flexible PCBs are generally more expensive to produce than rigid PCBs due to the complexity of their design and manufacturing process.
– Handling: Due to their flexibility, these PCBs can be more difficult to handle during the assembly process.
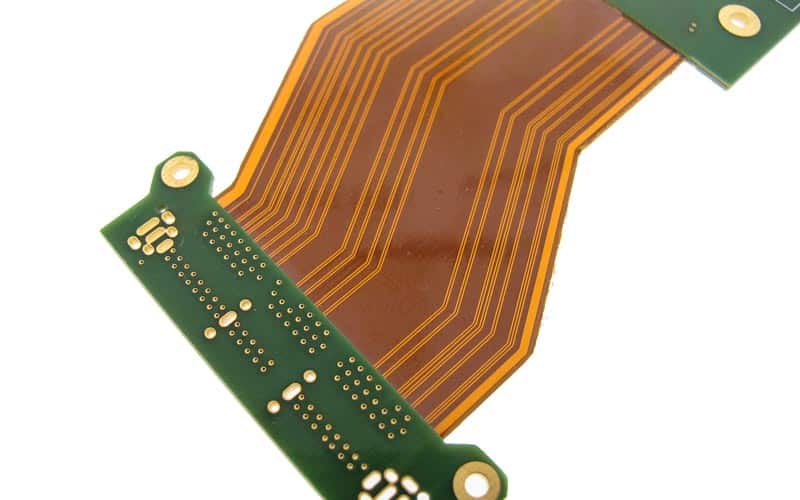
Rigid-Flex PCBs: The Best of Both Worlds
Rigid-Flex PCBs combine the advantages of both rigid and flexible PCBs, offering both flexibility and durability. They consist of multiple layers of flexible circuit substrates attached to one or more rigid boards. This design allows for a wide range of shapes, and the ability to be folded or curved while still providing a solid, rigid structure for components.
– Versatility: Rigid-Flex PCBs offer the benefits of both rigid and flexible PCBs, allowing for a wide range of shapes and designs.
– Durability: They provide a solid, rigid structure for components while still being able to withstand bending and folding, offering a unique combination of strength and flexibility.
– Space Efficiency: By combining rigid and flexible PCBs into one board, rigid-flex PCBs can save significant space, making them ideal for applications where space is at a premium.
Rigid-Flex PCBs are typically made from a combination of materials used in both rigid and flexible PCBs, such as FR-4 for the rigid sections and Polyimide for the flexible sections.
Rigid-Flex PCBs are used in a wide range of applications, including aerospace, automotive, medical, and consumer electronics, where the unique combination of rigidity, flexibility, and space efficiency can be leveraged.
Advantages
– Versatility: Rigid-Flex PCBs offer the benefits of both rigid and flexible PCBs, allowing for a wide range of shapes and designs.
– Durability: They provide a solid, rigid structure for components while still being able to withstand bending and folding.
– Space Efficiency: By combining rigid and flexible PCBs into one board, rigid-flex PCBs can save significant space.
Disadvantages
– Cost: Rigid-Flex PCBs are generally more expensive to produce than either rigid or flexible PCBs due to the complexity of their design and manufacturing process.
– Design Complexity: The design process for rigid-flex PCBs is more complex and requires careful consideration of the transition areas between the rigid and flexible sections.
Our Cutting-Edge PCB Manufacturing Equipment: Precision, Quality, and Efficiency
Explore our advanced PCB manufacturing equipment that enables us to transform your designs into high-quality, reliable PCB.
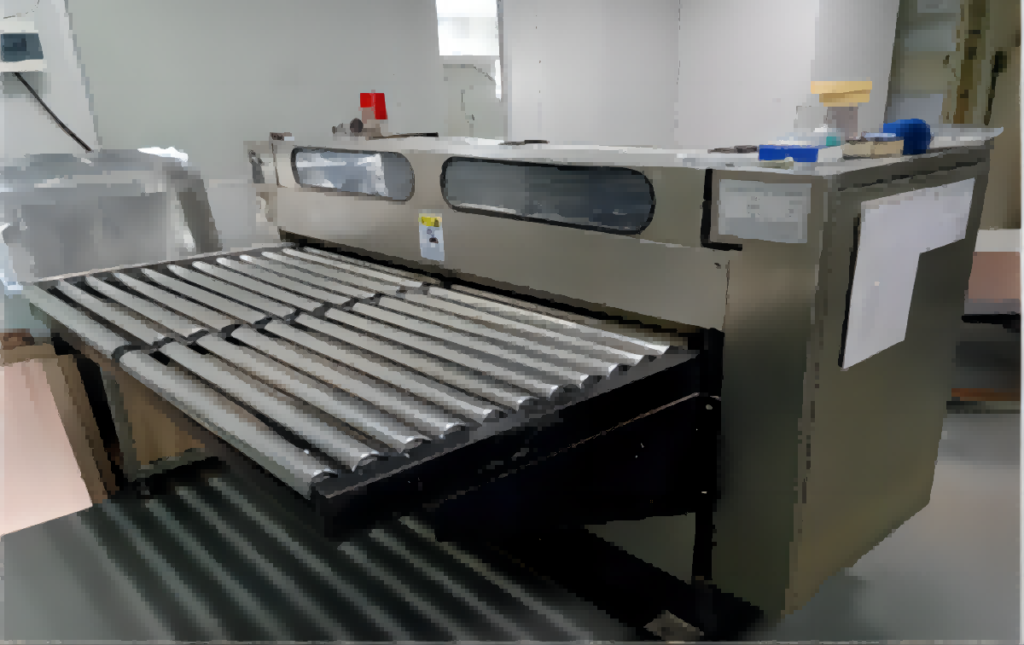
PCB Cutting Machine
Used for cutting the chosen material to the desired size.
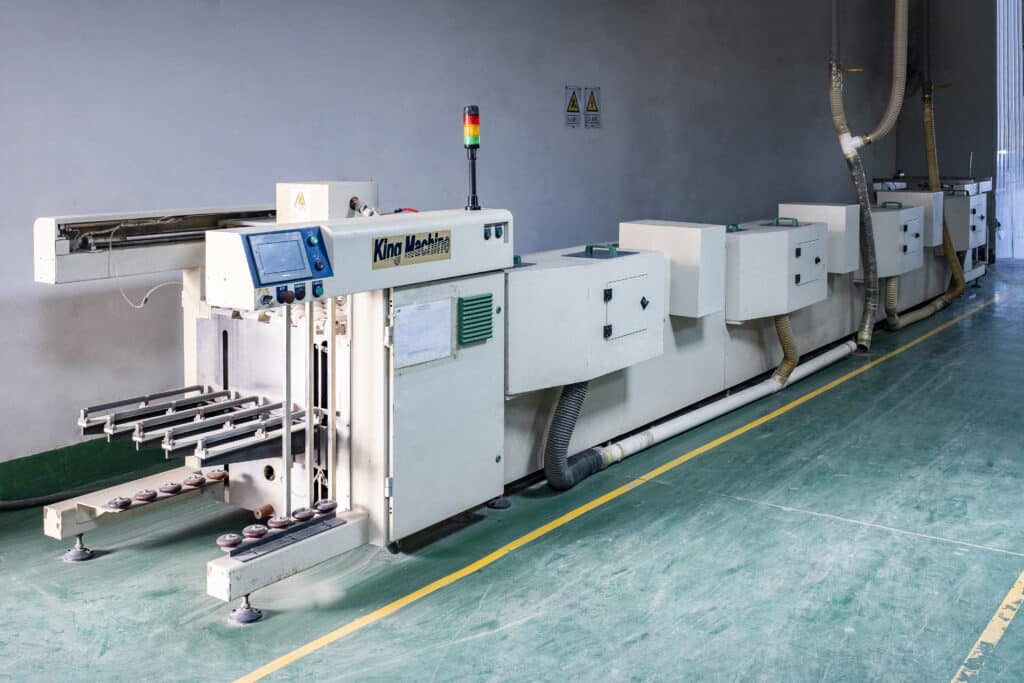
Automatic Edge Grinding Machine
Smooths the edges of the PCB.
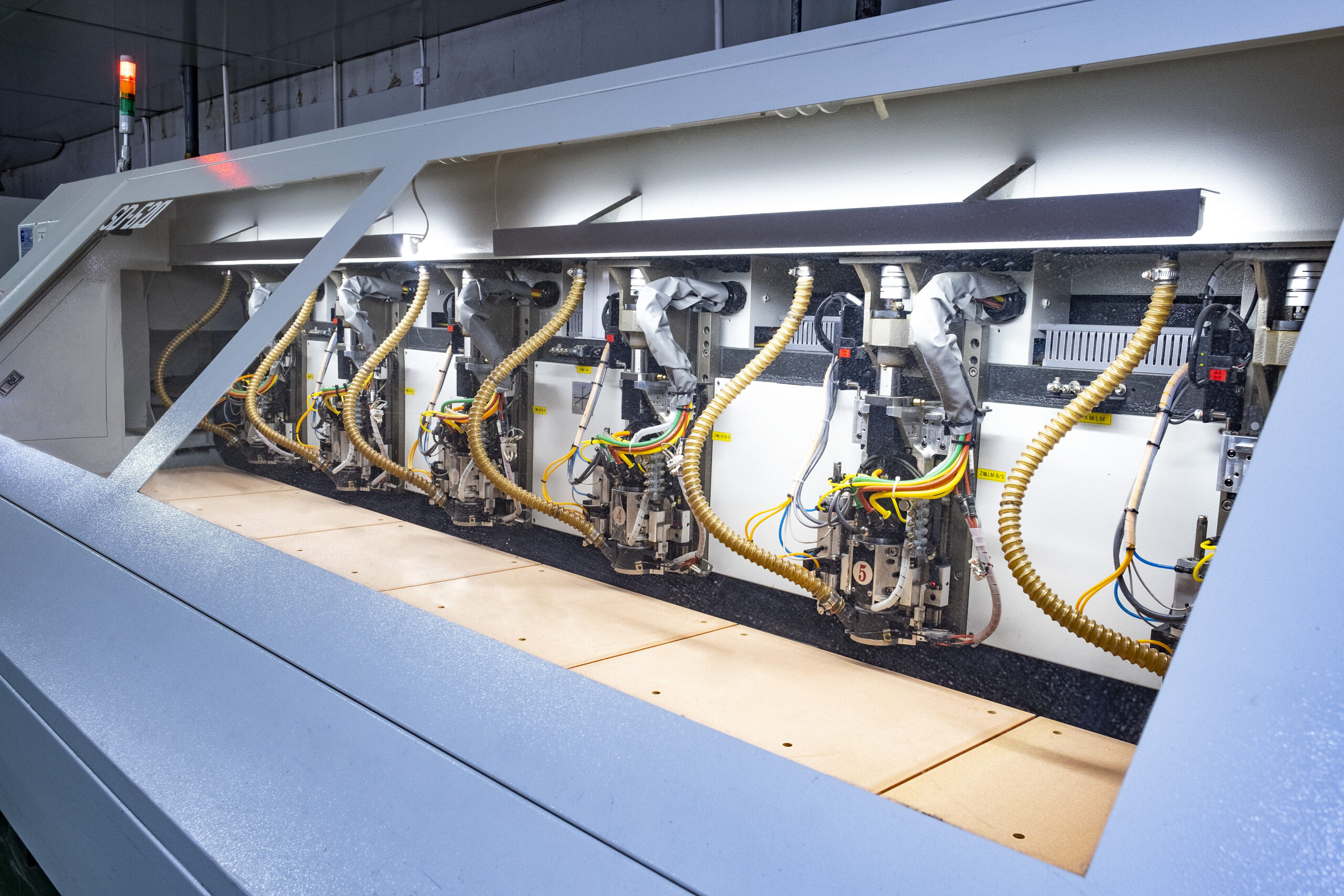
Automatic Drilling Machine
Precision drilling creates holes for component leads and vias.
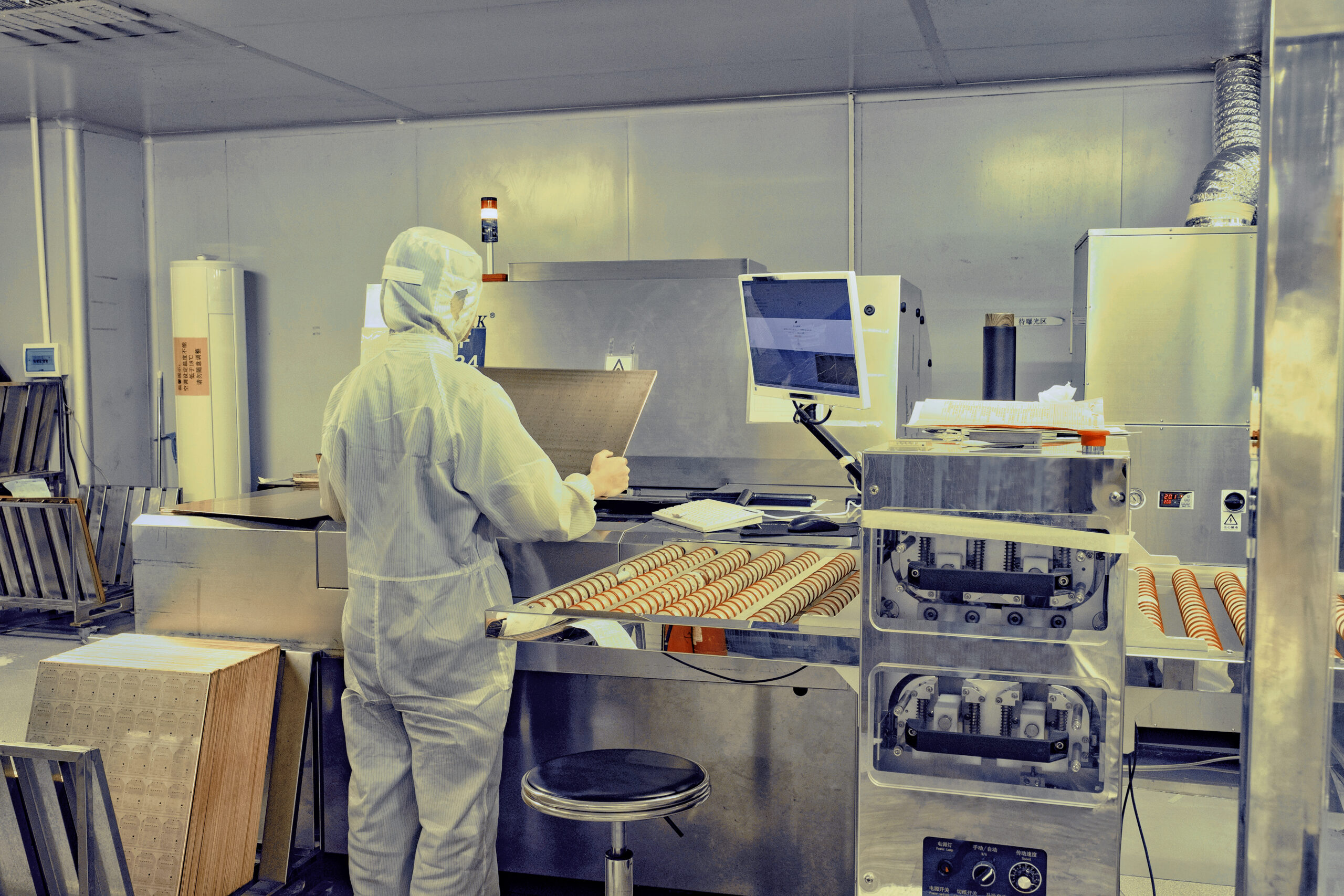
LDI Exposure Machine
Transfers the circuit pattern onto the PCB.
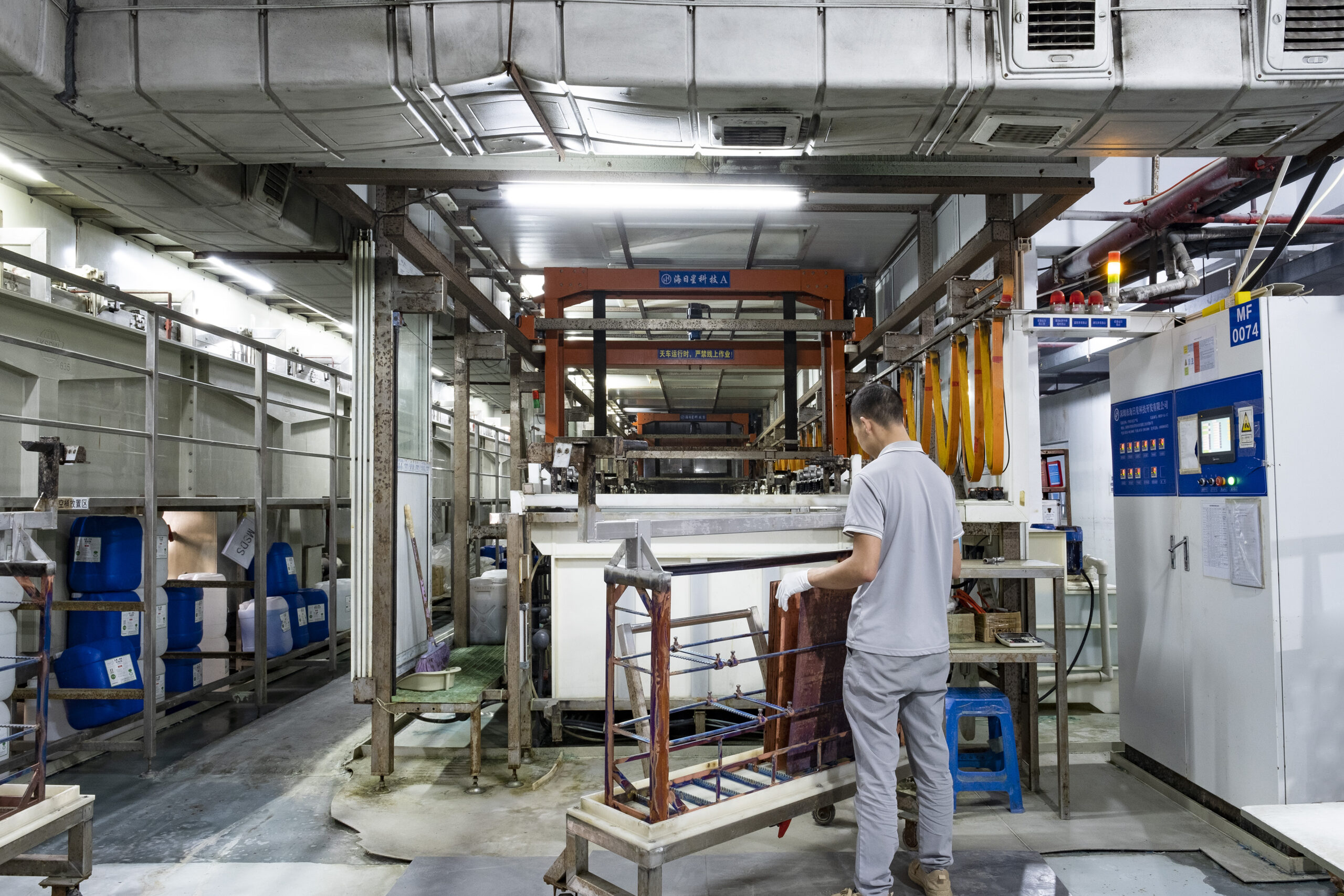
PTH Copper Deposition Line
Plates the drilled holes with copper to create electrical connections between the PCB's layers.
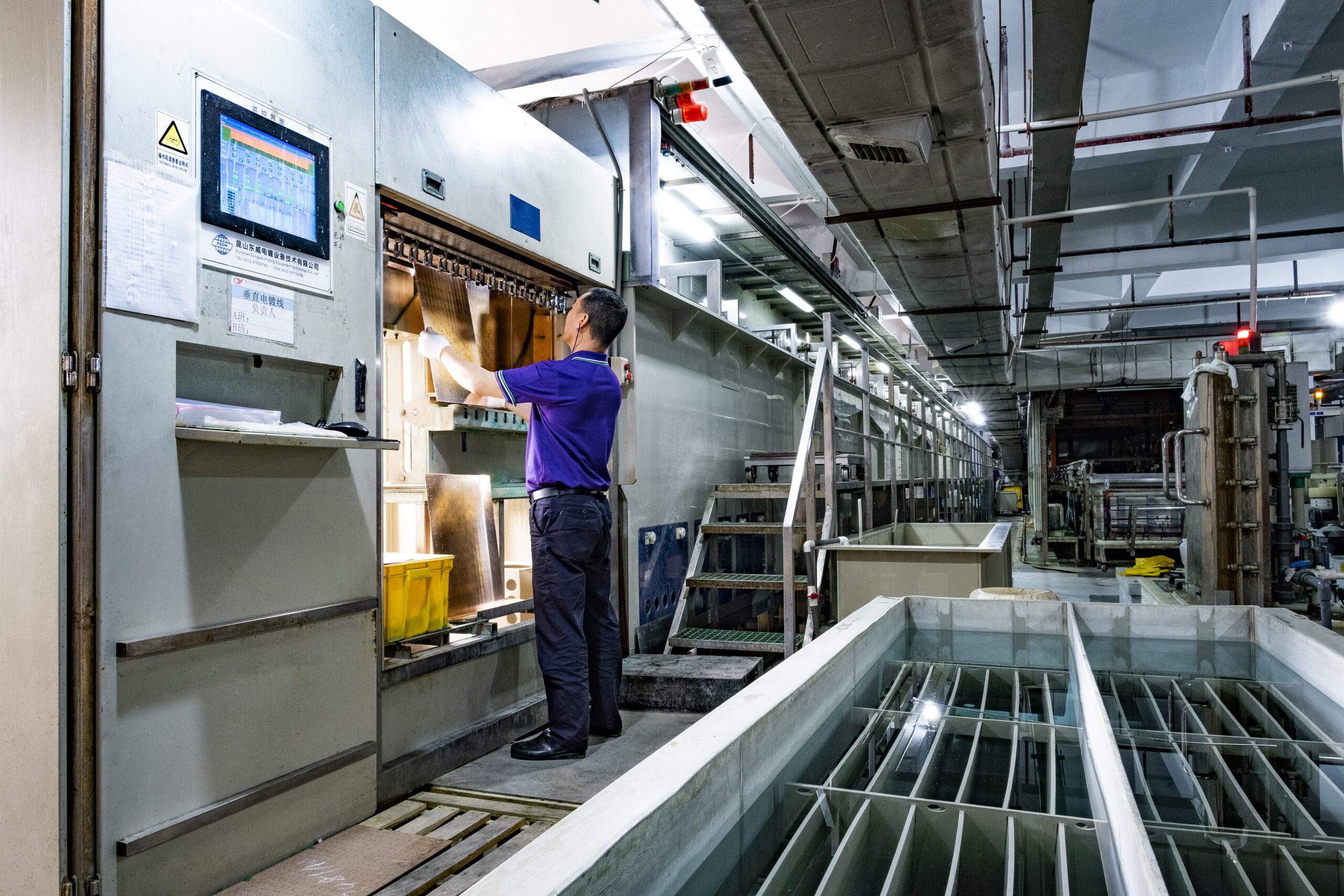
Vertical Continuous Electroplating (VCP) Line
Strengthens the copper connections through electroplating.
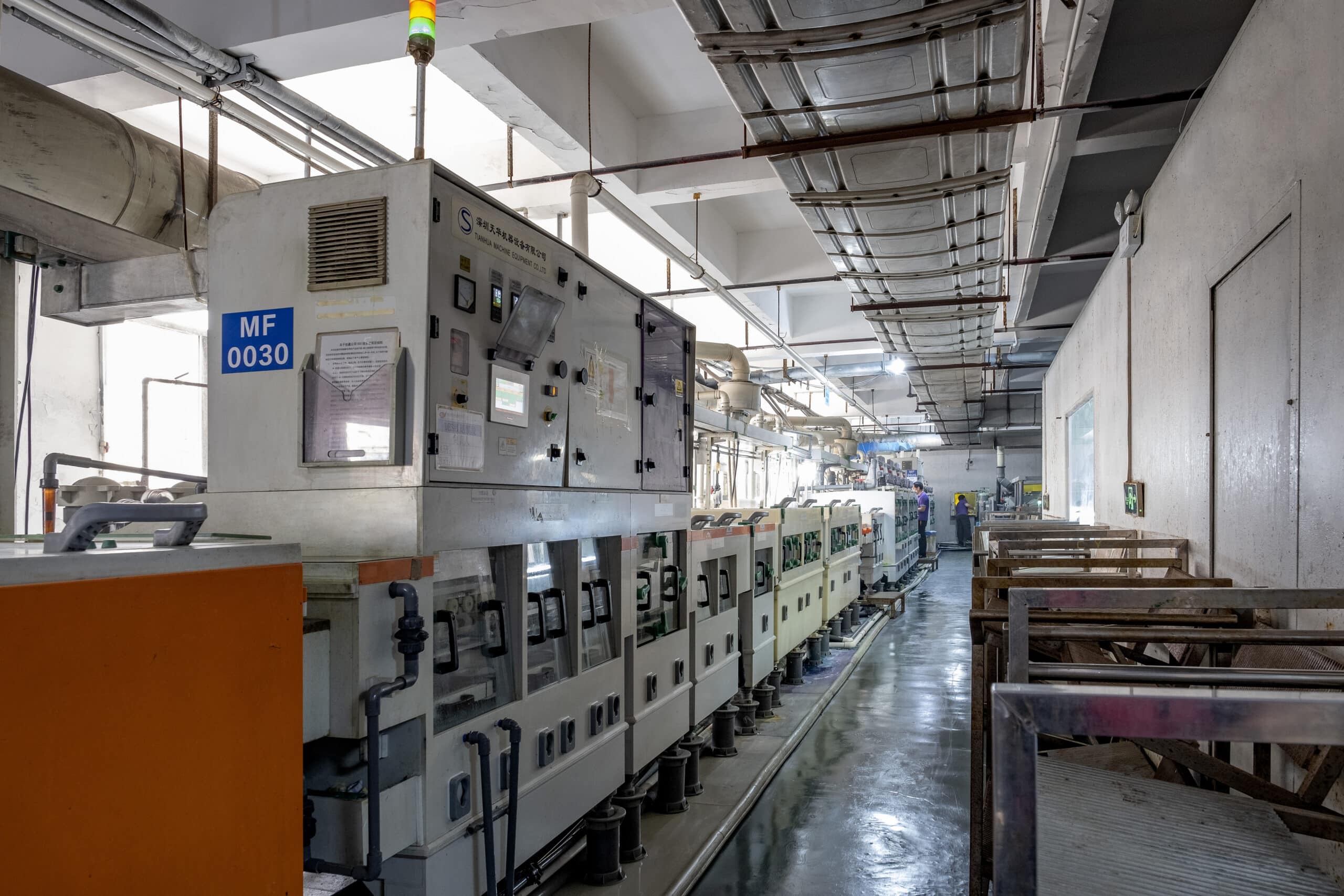
EDS Machine
Develops, etches, and strips the PCB to remove unwanted copper and leave behind the desired circuit pattern.
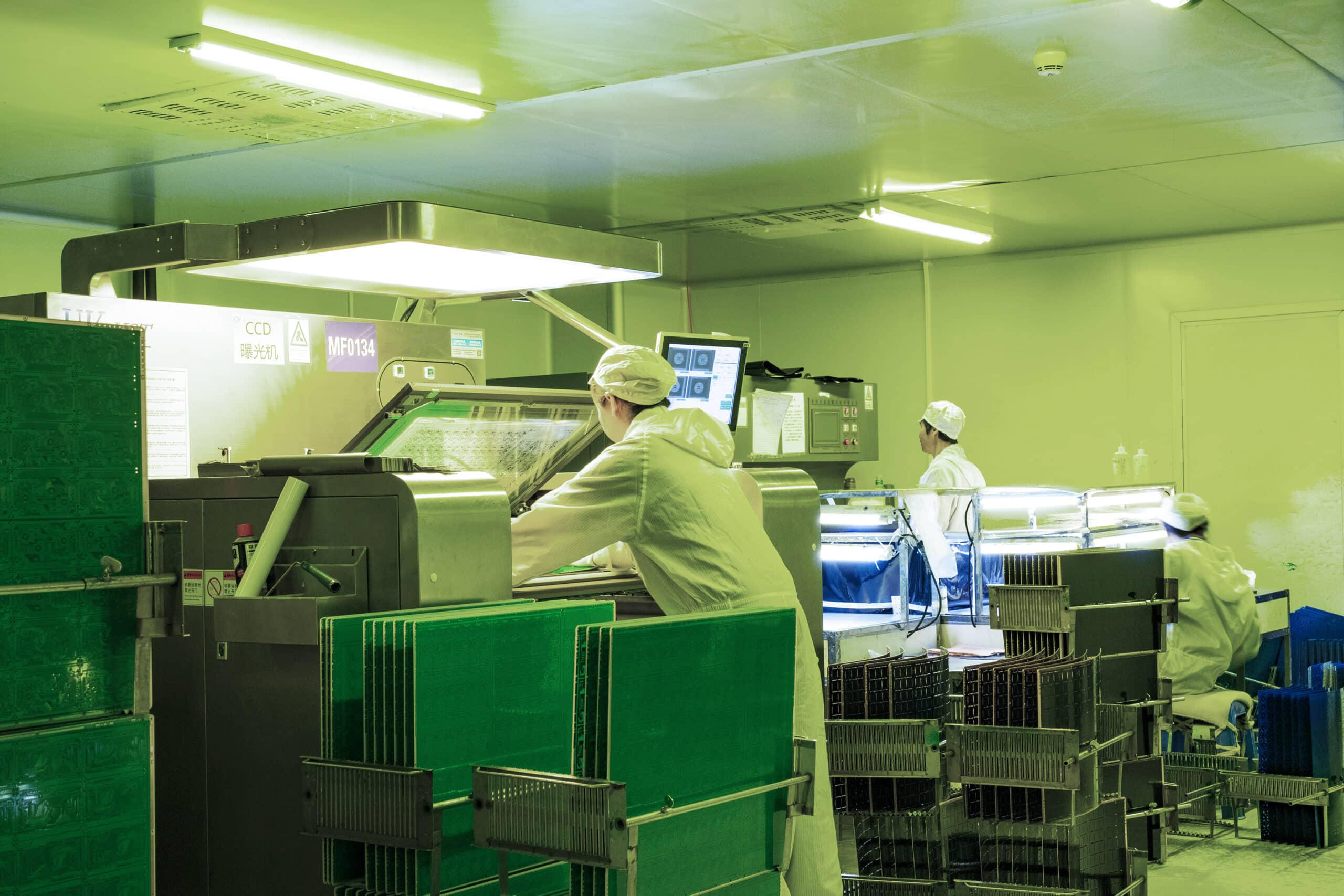
Solder Mask CCD Exposure Machine
Applies a solder mask to protect the copper from oxidation and prevent solder bridging during assembly.
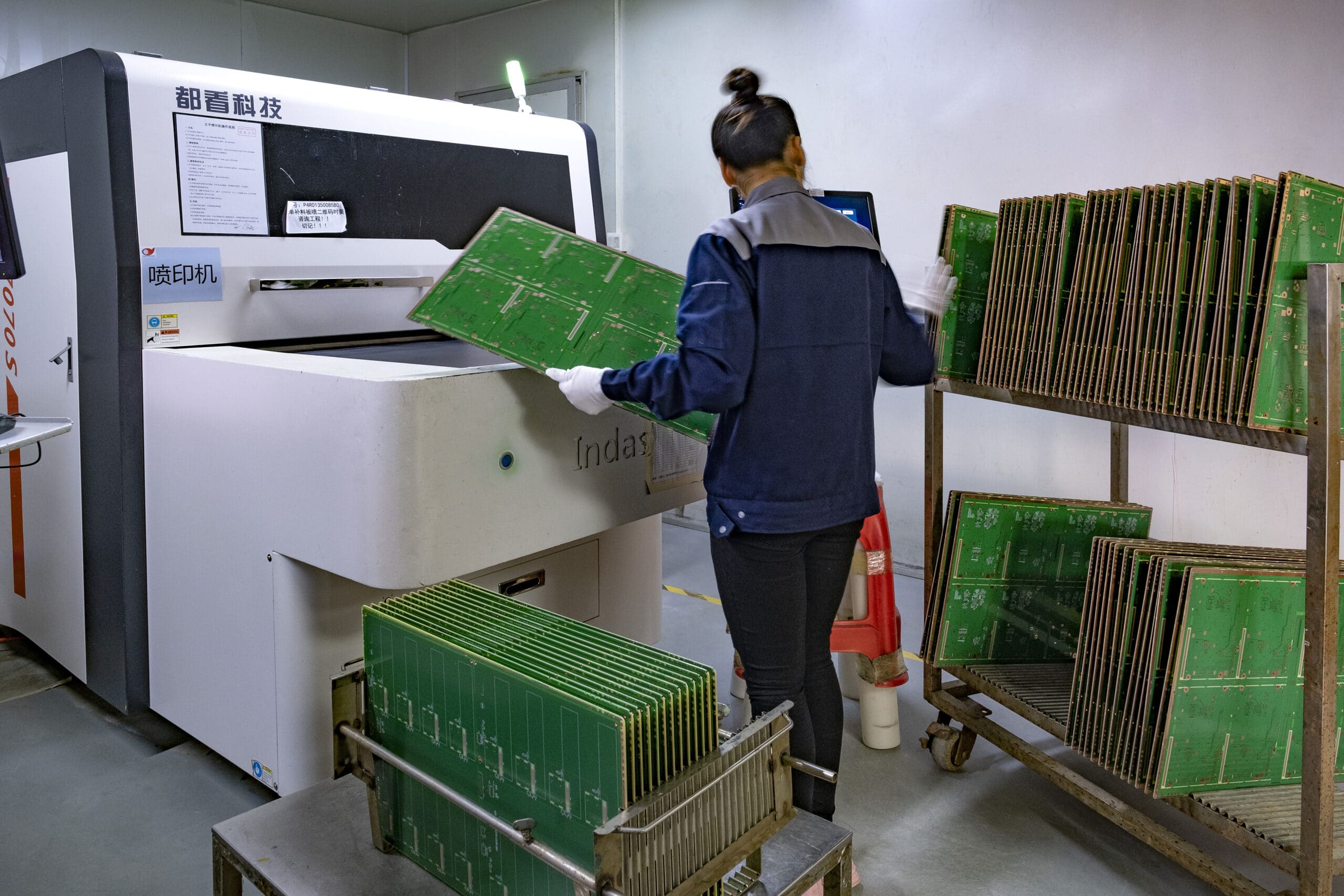
Automatic Text Printing Machine
Prints component identifiers and other markings onto the PCB.
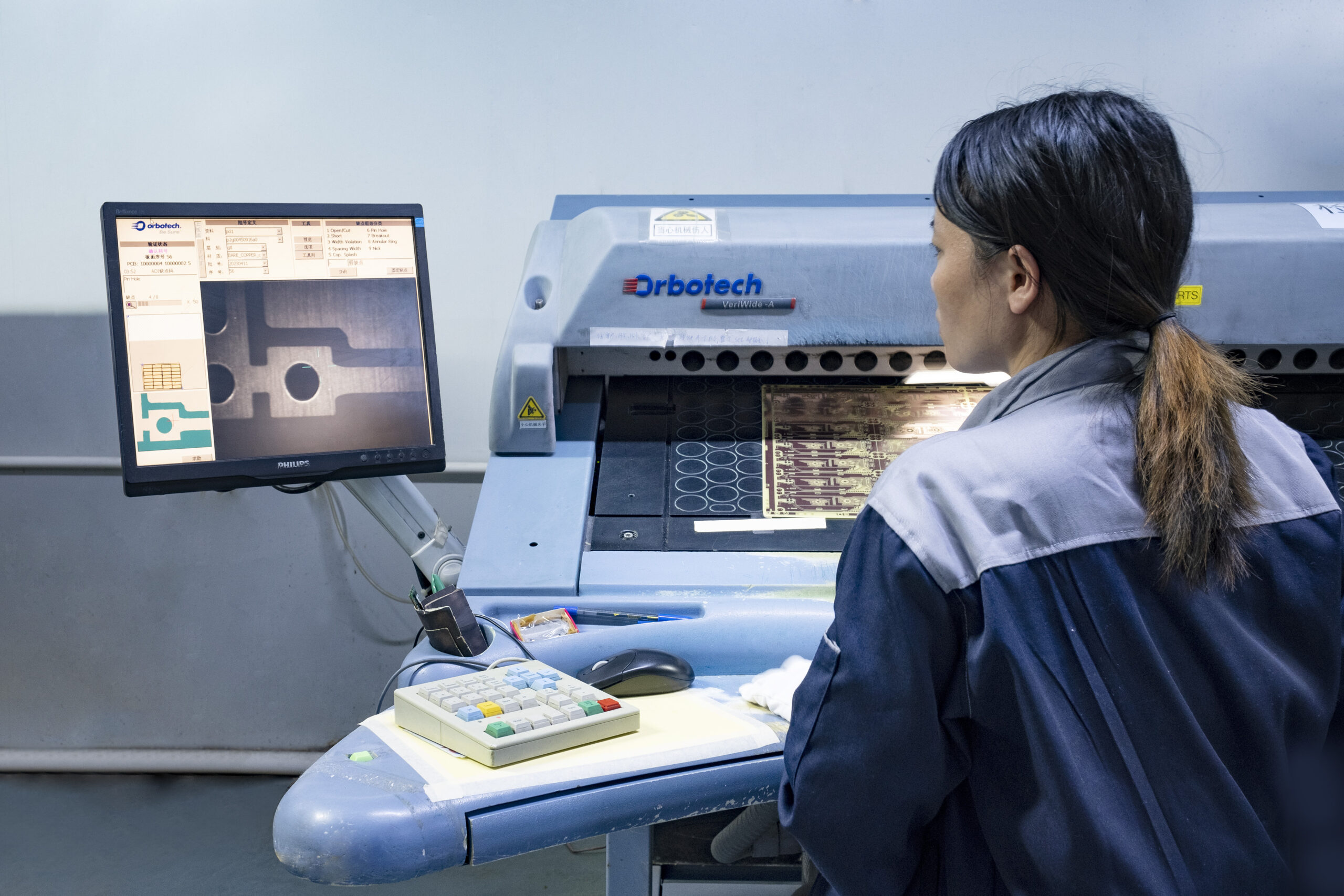
AOI Scanning Machine
Detects any potential defects or errors in each PCB.
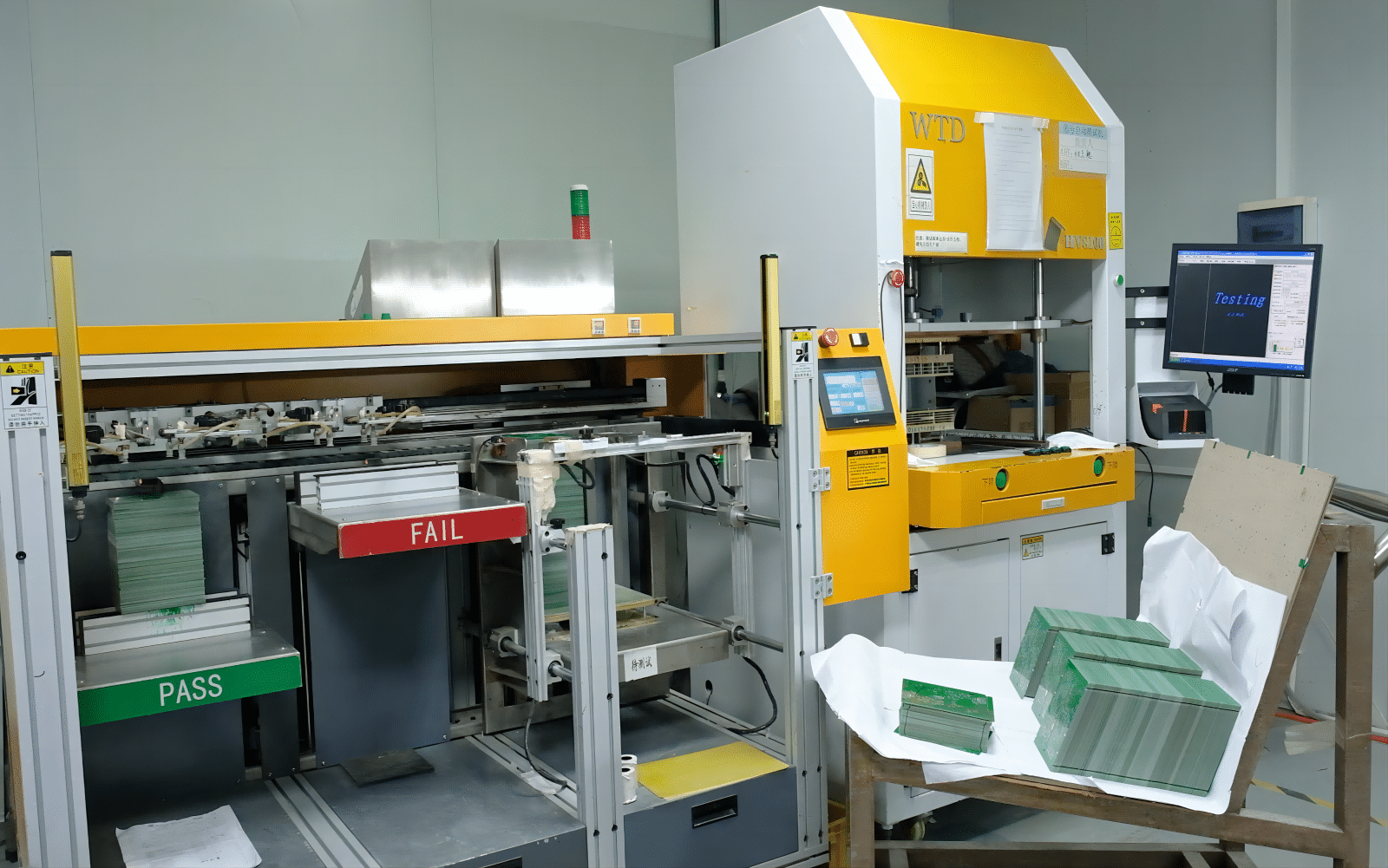
Automatic Testing Machine
Tests the PCBs to ensure they function as designed.
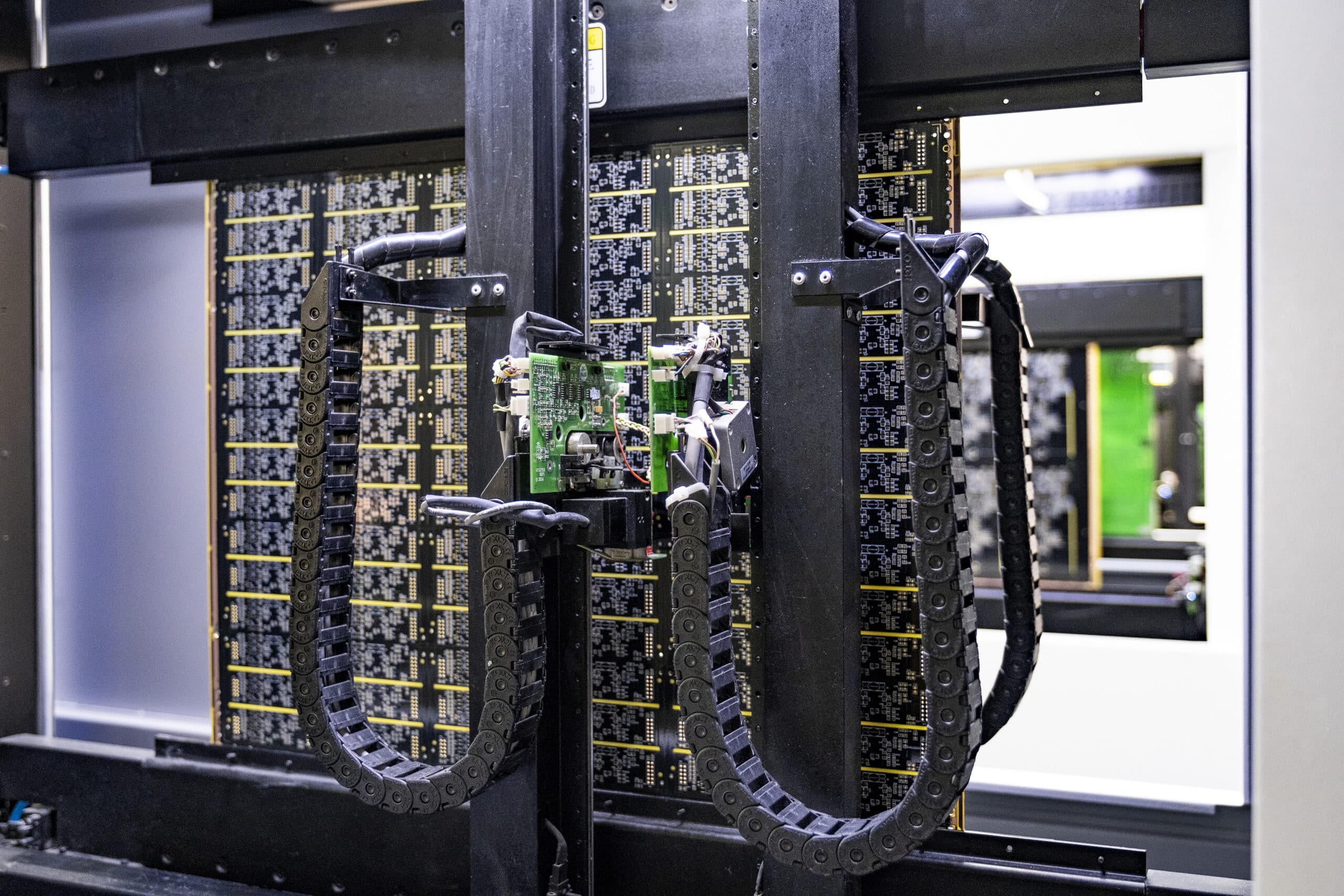
Flying Probe Tester
Used for further testing, particularly for low-volume, high-mix PCBs.
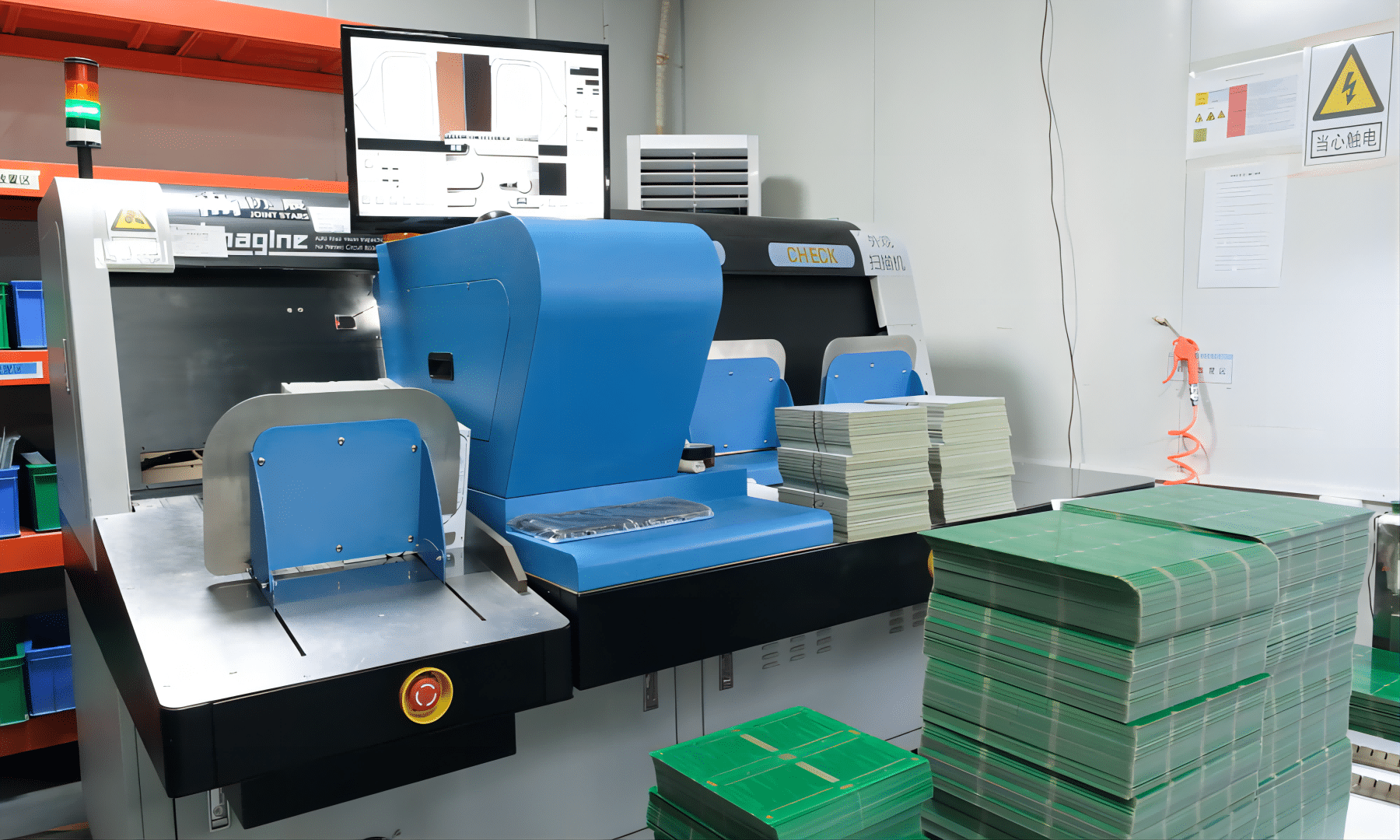
Visual Inspection Machine
Checks for any visible defects or anomalies in the PCBs.
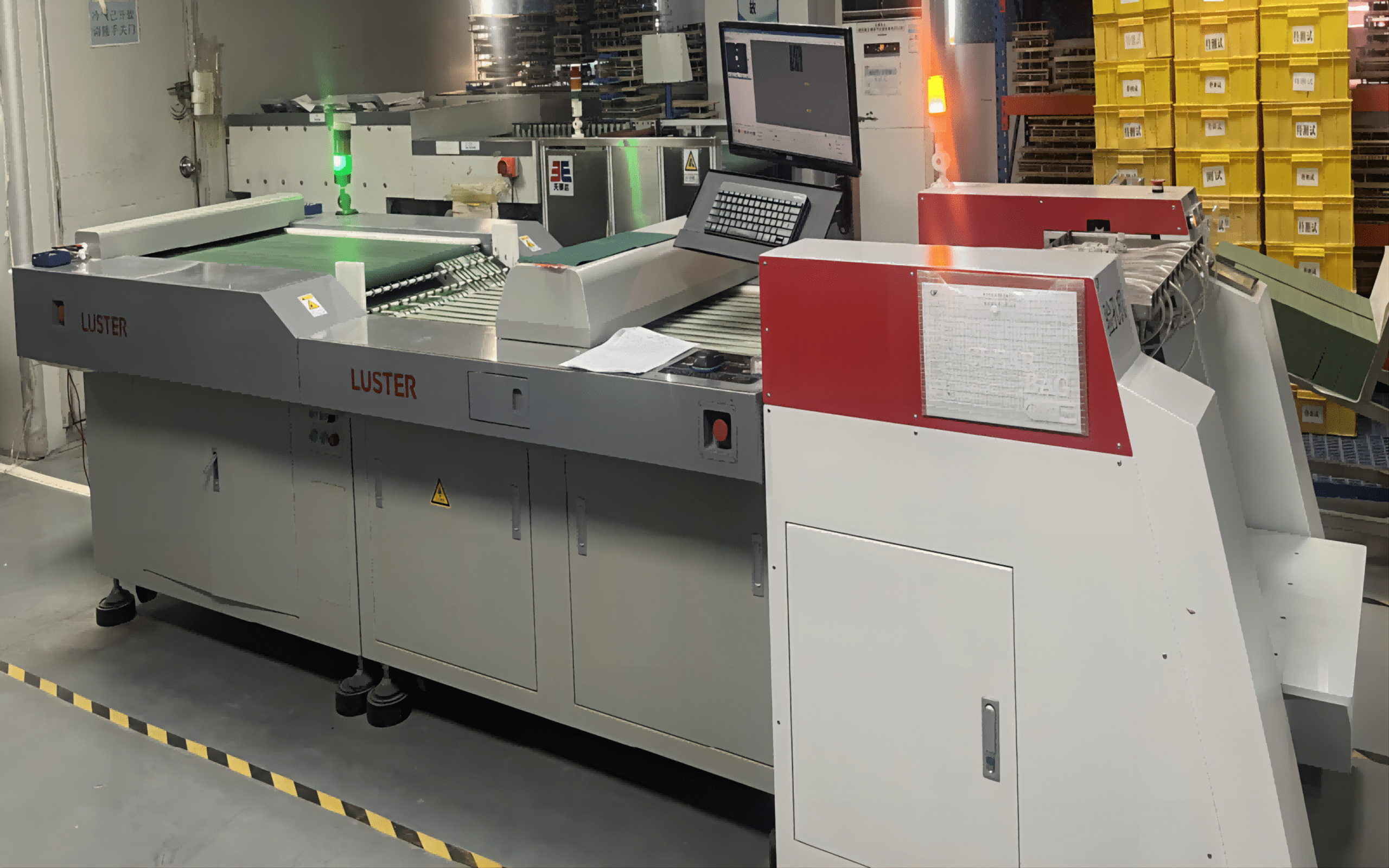
Hole Inspection Machine
A hole inspection machine is used to check the quality and accuracy of the drilled holes.
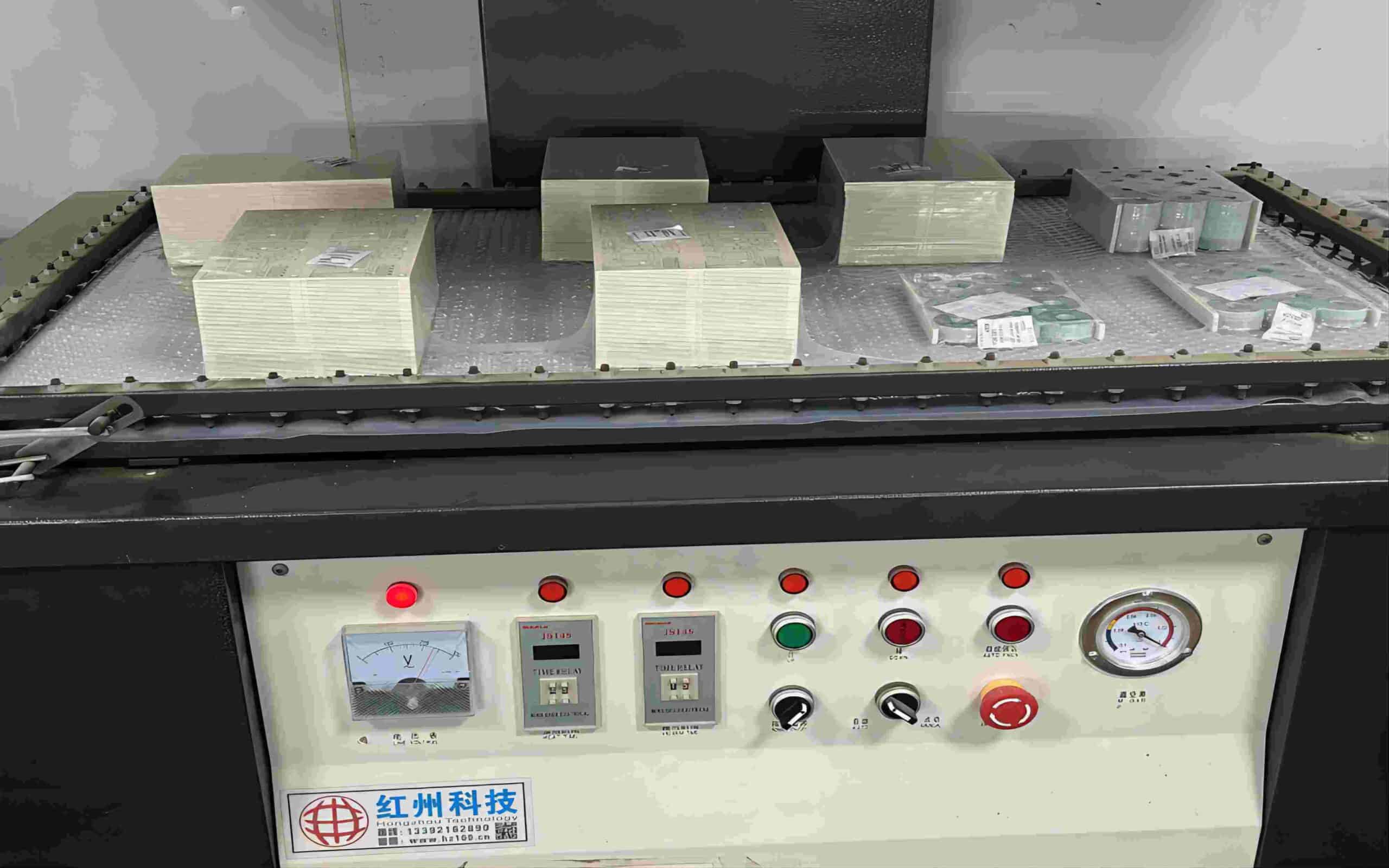
Packaging and Delivery
After passing all inspections and tests, the PCBs are carefully packaged for delivery.
ITEMS | Parameters (in metric) | Remarks | ||
Double side/Multi-layer | ||||
Max panel size | 32”×20”(800mm×508mm) | |||
Innerlayer line width/space(min) | 0.075m(3mil) | |||
Min ninnerlayer pad | 5min(0.13mm) | Pad annular (referring to the width of the solder ring) | ||
Min core thickness | 4min(0.1mm) | |||
Thickness of innerlater copper | 1/2oz(17um) | No copper cladding | ||
Thickness of outerlayer base copper | 1/2oz(17um) | |||
Thickness offinished panel | 0.20-4.0mm | |||
Tolerance of finished panel thickness | Thickness <1.0mm | ±12% | 4-8layers | |
1.0≤Thickness<2.0mm | ±8% | 4-8layers | ||
±10% | ≥10layers | |||
Thickness≥2.0mm | ±10% | |||
Surface treating process of innerlayer | Brown Oxide | |||
Layer count | 1-16L | |||
Registration of innerlayer to of innerlayer | ±3mil(±76um) | |||
Min diameter of finished hole | 0.2mm(8mil) excluding HDI | |||
Accuracy of hole position | ±2mil(±50um) | |||
Tolerance of drilled slot | ±3mil(±75um) | |||
Tolerance of PTH diameter | ±2mil(±50um) | |||
Tolerance of NPTH diameter | ±1mil(±25um) | |||
MaxA.R.of PTH | 10:01 | |||
PTH hole copper thickness | 0.4-2mil(10-50um) | |||
Image to image tolerance | ±3mil(0.075um) | |||
Outer layer line width/space(min) | 3mil/3mil(75um/75um) | |||
Tolerance of etching | ±1mil(±25um) | |||
Thickness of solder mask | Line end | 0.4-1.2mil(10-30um) | ||
lineComer | ≥0.2mil(5um) | |||
On Substrate | ≤finished Cu thickness+1.2mil(≤finished Cu thickness+30um) | |||
Hardness of solder mask | 6H | |||
Solder mask registration tolerance | ±2mil(±50um) | |||
Min solder mask dam | 3.0mil(75um) | |||
Max solder mask plug hole diameter | 0.6mm | |||
Surface freatment | ||||
HASL、gold finger、Au Panel、OSP、ENING | ||||
Range of nickel thickness for electroless nickel and immersion gold | 120u”/240u”(3um/6um) | |||
Range of gold thickness for electroless nickel and immersion gold | 2u”/6u”(0.05um/0.15um) | |||
Impedance control and tolerance | ±10% | |||
Peel strength of line | ≥61B/in(≥107g/mm) | |||
Warp and twist | ≤0.75% | |||
Blind Hole/buried plate | √ | |||
Surface Treatment | Immersion gold, immersion silver, immersion tin, OSP, spray pure tin, gold plating | |||
Substrate material | GETEK, ROGERS, Teflon, high TG, aluminum-based, FR-4 |
1-2L Lead-time | Sample Expedited 24 hours and 48 hours, Normal2-5 days, Mass production 5-7days |
4- 8L Lead-time | Sample Expedited 48 hours 72 hours, Normal 5-7days,Mass production 7-10 days |
10-18L Lead-time | 10-15 days,Special circumstances based on the actual PCB design |
More than 20L Lead-time | 15-20 days ,Special circumstances based on the actual PCB design |
Acceptable File Format | ALL Gerber Files、POWERPCB、PROTEL、PADS2000、CAD、AUTOCAD、ORCAD、P-CAD、CAM-350、CAM2000 etc. |
Steering Clear of Common Pitfalls in PCB Manufacturing
At Rowsum, we not only identify potential challenges in PCB manufacturing but also provide effective solutions to ensure a smooth and successful production process. Here are some common pitfalls and how we help you navigate them for optimal results.
Design Errors
Design errors can range from incorrect component placement to improper trace routing, leading to functional issues in the final product. At Rowsum, we conduct a thorough design review before manufacturing begins. Our experienced engineers scrutinize every detail of your design to catch and correct potential errors, saving you time and money.
Incorrect Board Thickness
Selecting the wrong board thickness can lead to issues like poor fit with the device casing or mechanical instability. At Rowsum, we guide our customers in choosing the right board thickness based on their specific application and requirements, ensuring a perfect fit and optimal performance.
Manufacturing Defects
Manufacturing defects such as solder bridging, misaligned components, or poor hole quality can compromise the functionality and reliability of your PCBs. Rowsum's rigorous quality control processes, including AOI scanning and flying probe testing, help to prevent these issues and ensure that every PCB we deliver meets our high-quality standards.
Lead Time Delays and Expedited Services
Delays in the manufacturing process can disrupt your project timeline and potentially increase costs. At Rowsum, we understand the importance of on-time delivery. Our efficient manufacturing processes and dedicated project managers ensure that your PCBs are delivered on schedule. For projects with tight deadlines, we offer expedited services to meet your needs. By prioritizing your order and optimizing our production schedule, we can significantly reduce the lead time. However, it's crucial to communicate your timeline requirements to us as early as possible, so we can plan accordingly.
Estimated Delivery Times
We understand that knowing when your order will arrive is important for planning and managing your project. That's why we provide estimated delivery times based on our production schedule and the shipping method chosen. Our project managers will keep you informed about the progress of your order and provide updates on the expected delivery date.
Communication Issues
Clear and consistent communication is crucial in any PCB project. Misunderstandings or lack of information can lead to errors and delays. At Rowsum, our dedicated project managers ensure seamless communication. They keep you informed at every stage of the process and promptly address any concerns you may have.
Want to know more about how Rowsum can help streamline your PCB projects?
Get in touch with our experts to discuss your specific needs and learn how our tailored solutions can drive your project success.
Explore Our Blog and Knowledge Base
Dive deeper into the world of PCB manufacturing with our comprehensive blog and knowledge base. From detailed guides and how-tos to industry insights and tips, we’ve got you covered. Stay informed and up-to-date with Rowsum’s expertly curated content.

Top 10 PCB manufacturers in Turkey
Introduction Need to find a PCB manufacturer in Turkey? You’ve come to the right spot. I’ve looked around and put together a list of the
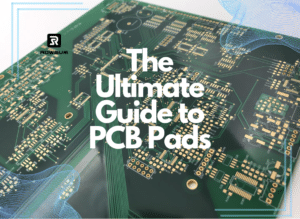
What Are PCB Pads? The Ultimate Guide to Types, Uses, and Design Tips
Introduction Imagine constructing an intricate Lego masterpiece without the small connectors that hold each piece in place. Frustrating, right? Now, picture these connectors failing at
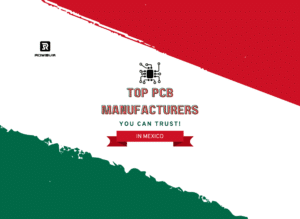
Top 10 PCB Manufacturers in Mexico – Reliable and High-Quality Suppliers
Introduction Finding the right Printed Circuit Board (PCB) manufacturer can be challenging in today’s competitive electronics manufacturing industry. But don’t worry—I’ve got you covered! Mexico
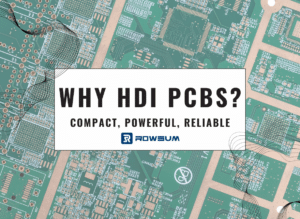
How Do HDI PCBs Enhance Device Performance and Reliability? See the Difference They Make!
Introduction to HDI PCB Technology: What You Need to Know Are you looking to enhance your electronic products with more functionality packed into a smaller
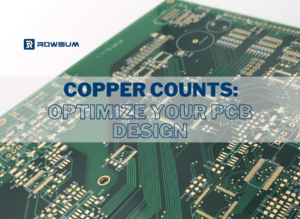
The Essential Guide to Copper Thickness for Optimal PCB Design
Introduction Navigating through the world of PCB design, you might have stumbled upon varying terms for copper thickness: 1OZ, 35um, 1.4mils. What do these numbers
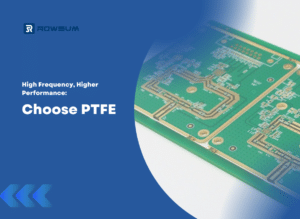
Are Traditional FR4 Boards Obsolete in the Face of PTFE PCBs?
Introduction Ever wondered why PTFE PCBs are the go-to choice for high-frequency applications? What sets them apart from the conventional FR4 boards in the competitive
Success Stories and Client Testimonials
Explore how we’ve empowered businesses with our PCB solutions and hear directly from our satisfied clients about their Rowsum experience.
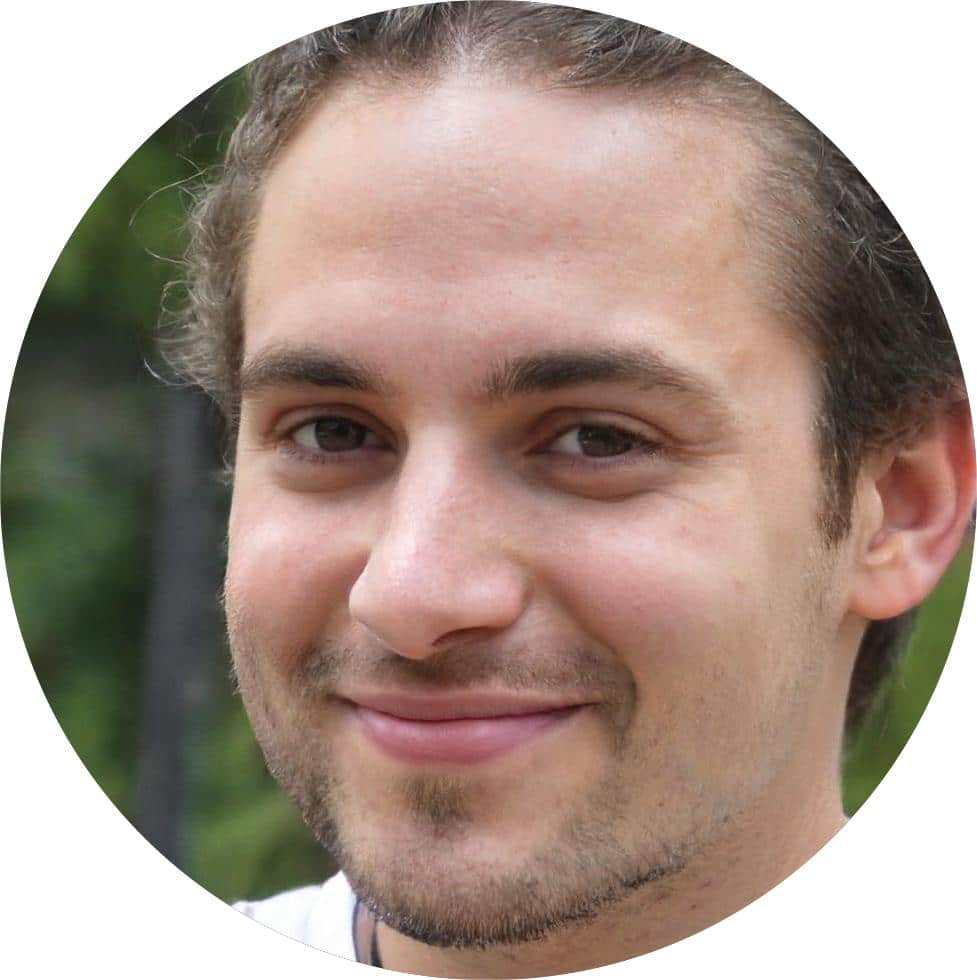
A U.S. tech startup was about to launch a new IoT device, but faulty PCBs from their previous supplier threatened to derail their plans. They turned to Rowsum for help.
Our U.S. business manager, Leo, quickly coordinated with our manufacturing team in China. We identified a design flaw in the PCBs, corrected it, and produced a new sample. After the startup approved the design, we immediately started mass production.
Despite the tight schedule, we delivered high-quality, error-free PCBs in time for the product launch. The startup was impressed with our quick response, attention to detail, and commitment to quality. They said, “Rowsum saved our product launch. Leo was particularly helpful and ensured everything went smoothly.”
Maria
“I’ve been in procurement for over a decade, and Rowsum is hands down the best PCB supplier I’ve worked with. Their attention to detail and customer service are top-notch. They’ve made my job a lot easier!”
Sophia
“As a startup, we were looking for a PCB supplier who could work with our tight budgets and timelines. Rowsum has been a perfect fit. Their competitive pricing, fast turnaround times, and excellent customer service have made them an invaluable partner in our growth journey.”
Lucas
“Working with Rowsum has been a breath of fresh air. They’ve helped us troubleshoot design issues and optimize our PCBs for manufacturing. It’s clear they know their stuff. A big thumbs up from our engineering team!”
Why Choose Rowsum for Your PCB and PCBA Needs?
Experience the Rowsum Difference: Quality, Innovation, and Customer-Centric Solutions
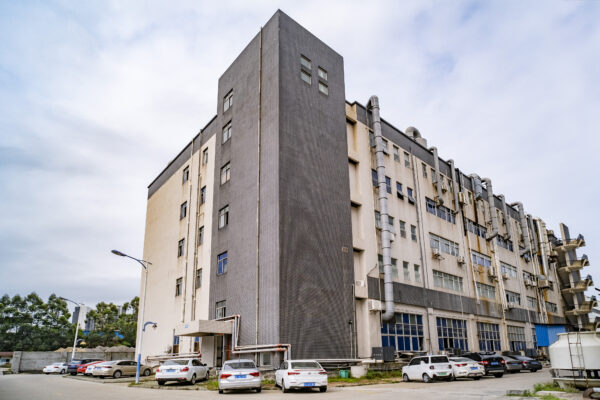
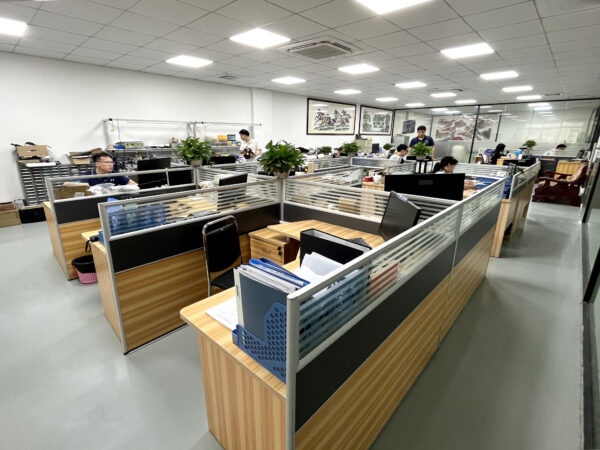
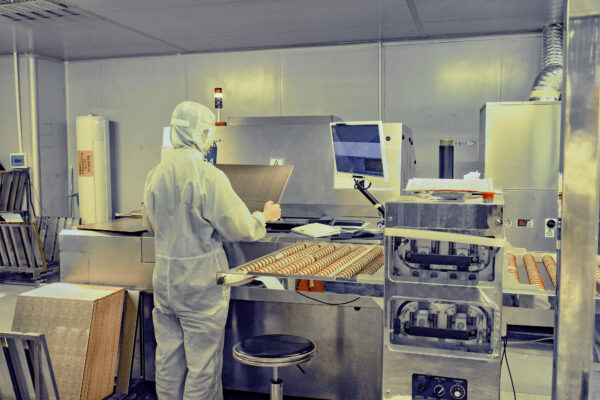
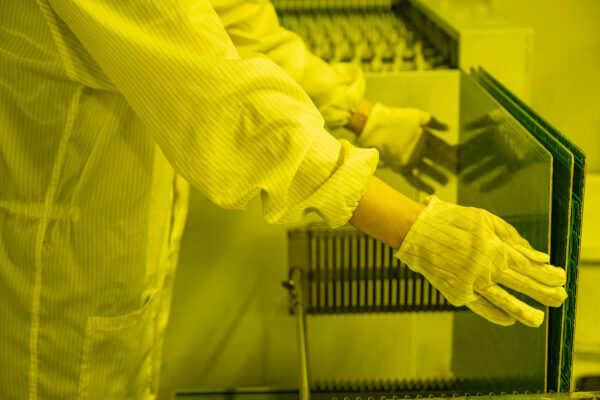
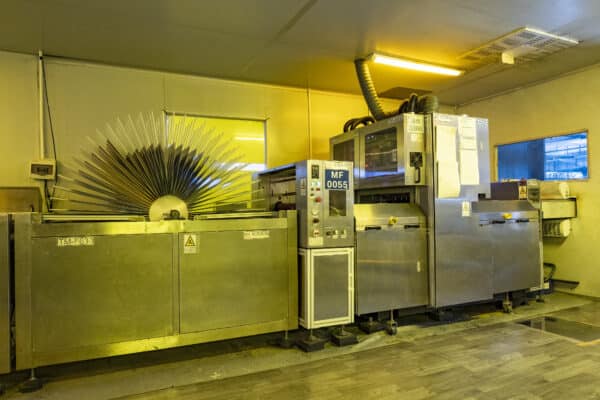


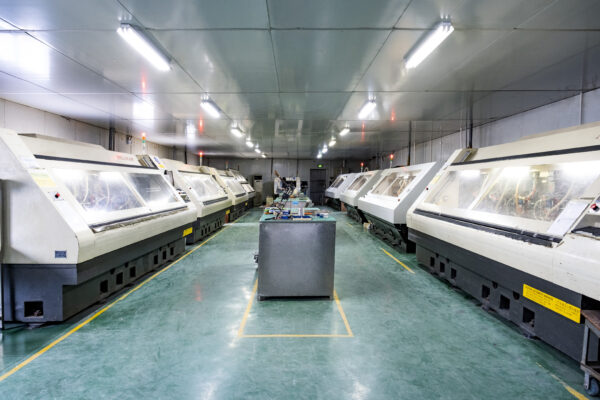
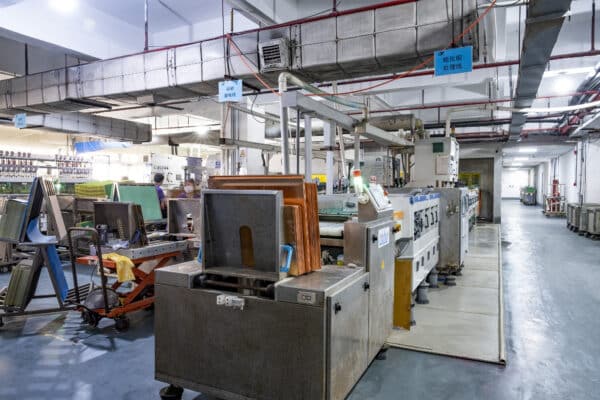
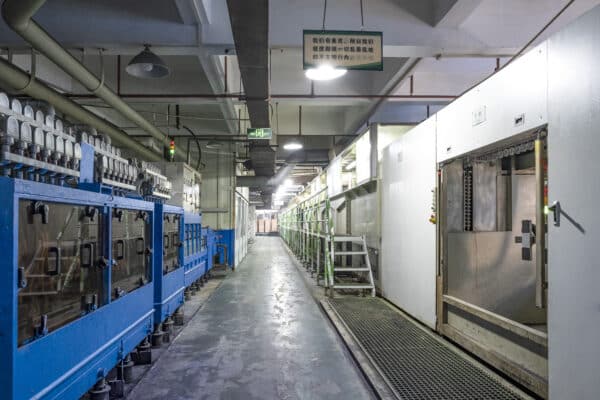
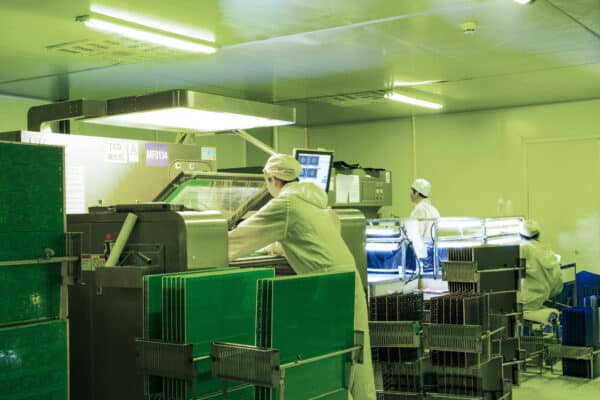
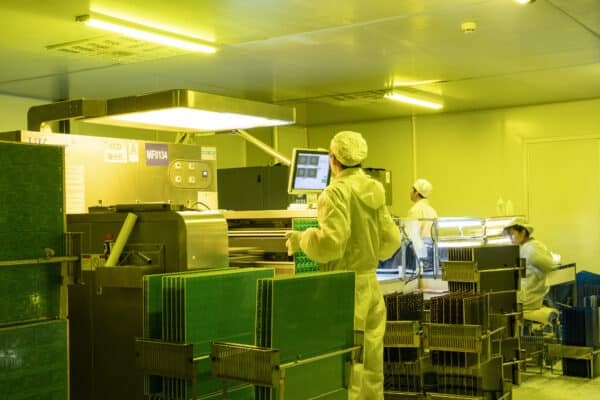
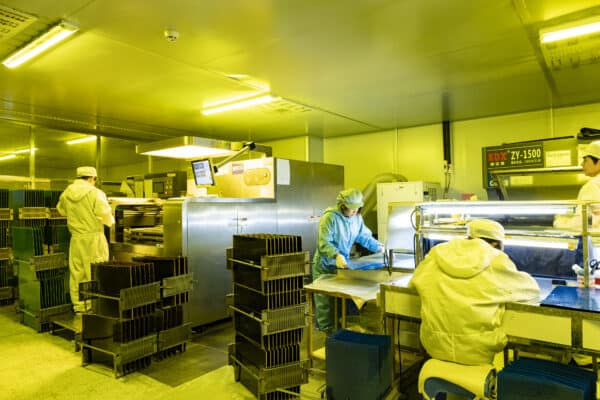
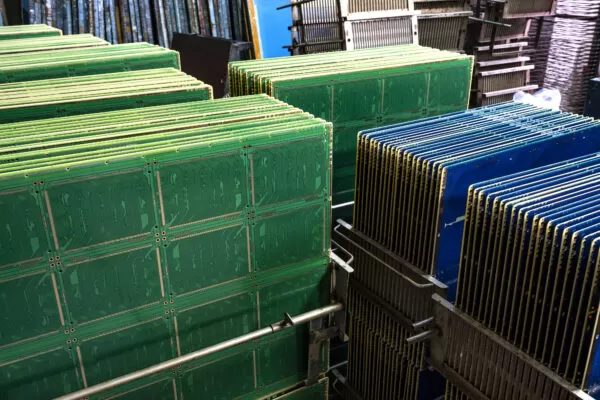
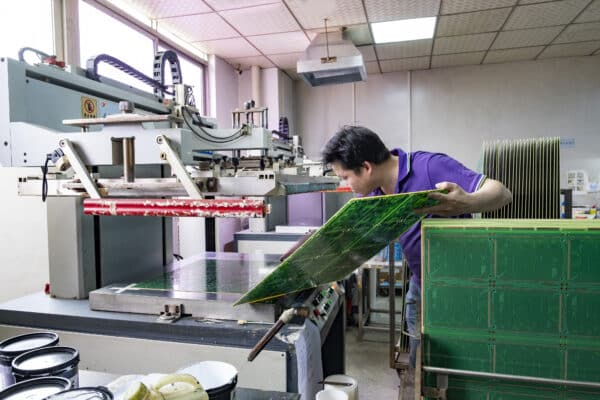
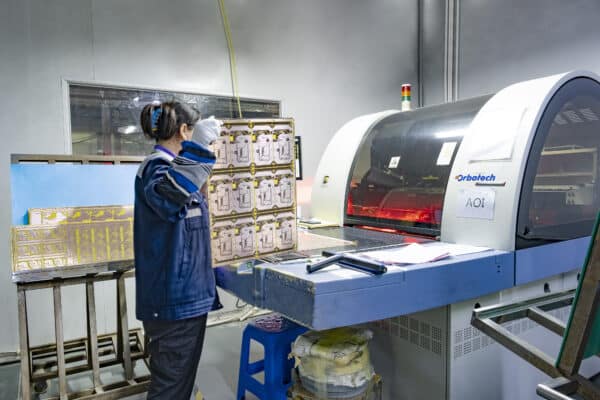
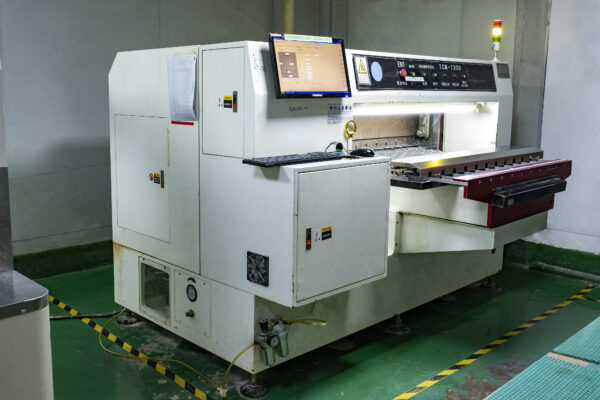
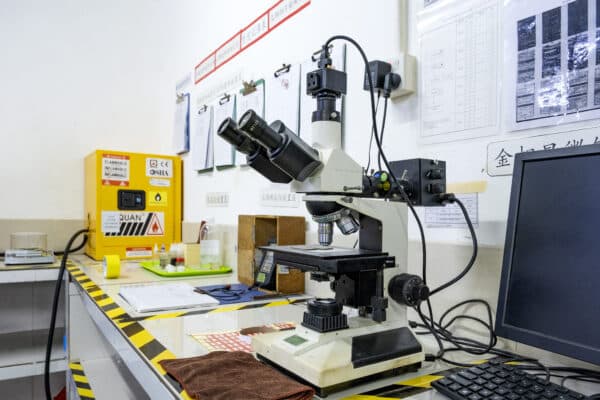
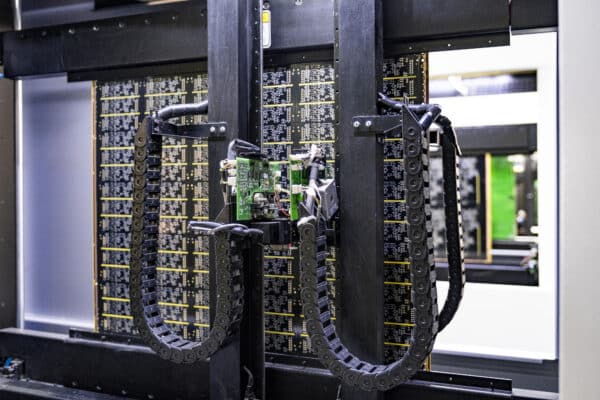
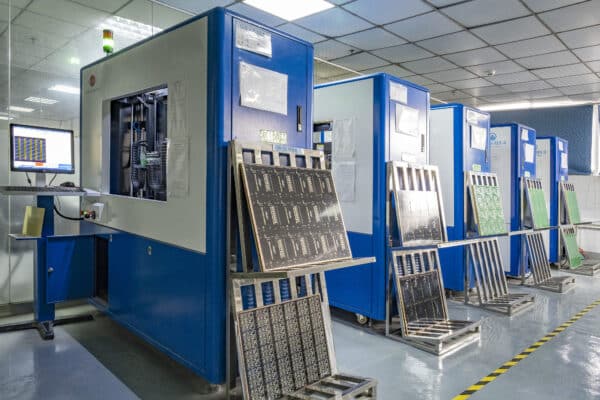
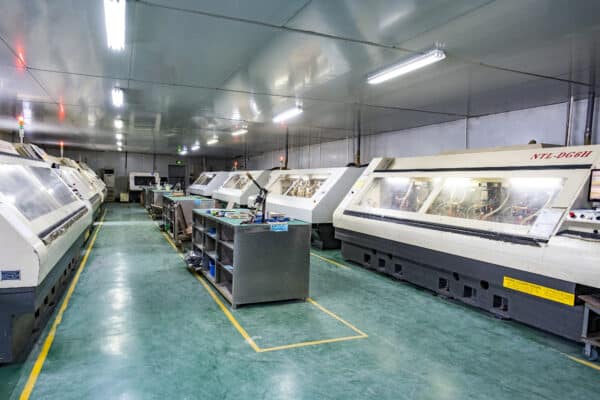
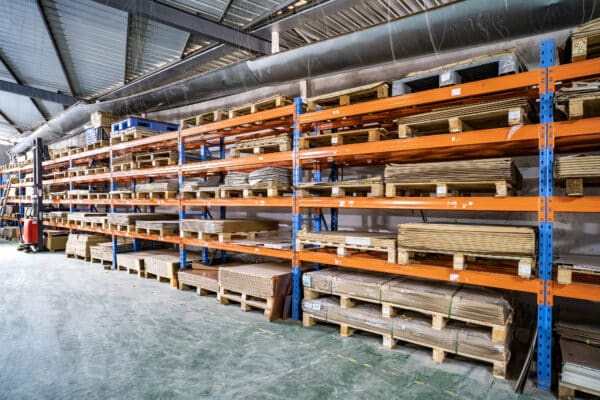
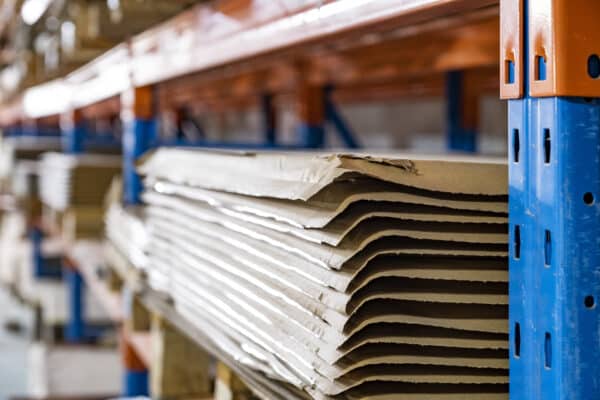
Rowsum has been a trusted partner for businesses worldwide, providing high-quality PCB and PCBA products for over 30 years. Our dedication to innovation, top-notch quality, and unrivaled customer service has earned us a reputation as a leading PCB manufacturer in the industry. Here’s why you should choose Rowsum for your next PCB project:
- Customer-Centric Solutions: At Rowsum, we prioritize our customers’ needs and work closely with them to provide tailored PCB and PCBA solutions that perfectly fit their unique requirements. Our commitment to understanding your business goals allows us to deliver PCB products that not only meet but exceed your expectations.
- Cutting-Edge Technology and Manufacturing Excellence: Rowsum utilizes state-of-the-art production facilities and cutting-edge technology to manufacture PCBs that satisfy both current and future demands. Our automated production line ensures efficient and cost-effective delivery of high-quality PCB and PCBA products. With Rowsum, you’re investing in a company that stays at the forefront of technological advancements.
- Quality, Reliability, and Customer Service: Our dedication to quality, reliability, and customer service sets us apart from the competition. We understand the pain points faced by our clients, such as high prices, inconsistent product quality, and lack of reliable customer service. Rowsum addresses these concerns by offering competitive pricing, top-quality products, and exceptional customer support.
- Transparent and Confidential Collaboration: Rowsum values transparency and confidentiality in our business relationships. We prioritize open communication, keeping our clients informed throughout the entire manufacturing process while safeguarding their sensitive information. When you choose Rowsum, you’re choosing a partner you can trust.
In conclusion, Rowsum is the ideal choice for businesses seeking a PCB and PCBA manufacturer that offers customer-centric solutions, cutting-edge technology, and a commitment to quality and reliability. Experience the Rowsum difference and let us bring your PCB projects to life with efficiency, cost-effectiveness, and exceptional customer service.”
Frequently Asked Questions
Your Queries Resolved About Our PCB and PCBA Services
What are the essential aspects of PCB design?
The critical aspects of PCB design include component placement, routing, power and ground planes, signal integrity, thermal management, and design for manufacturability (DFM).
What are the common PCB materials used in the industry?
Some common PCB materials include FR-4 (most widely used), polyimide, Rogers, aluminum-based, and ceramic-based substrates.
What are some common issues in PCB manufacturing and how are they addressed?
Common issues in PCB manufacturing include etching errors, drilling inaccuracies, solder mask misalignment, and contamination. These issues are addressed through rigorous quality control measures, including visual inspection, automated optical inspection (AOI), and electrical testing.
How do you ensure the quality of PCBs during manufacturing?
Quality assurance measures include visual inspection, automated optical inspection (AOI), X-ray inspection, and electrical testing (such as flying probe testing or in-circuit testing) to identify and rectify any defects.
What factors should be considered when selecting the appropriate PCB packaging?
The main factors to consider include the size and shape of the PCBs, protection from physical damage, electrostatic discharge (ESD) protection, and ease of handling during transportation and storage.
What are the best practices for PCB logistics and transportation?
Selecting the appropriate transportation method based on shipment size, destination, and delivery timeline is crucial. Options include courier services, air freight, sea freight, and rail freight. Proper packaging and handling during transit are also essential to ensure PCBs arrive in perfect condition.
How should PCBs be stored in a warehouse?
PCBs should be stored in a temperature and humidity-controlled environment, using ESD-safe packaging materials and implementing ESD protection measures. Organized storage methods, such as FIFO (First In, First Out), and proper shelving that prevents bending or warping should also be employed.
How should unpacked PCBs be handled and stored?
Always follow ESD-safe practices when handling PCBs and store them in a clean, organized workspace. For short-term storage, place unpacked PCBs on ESD-safe trays or racks, ensuring they are adequately supported and not subjected to excessive stress.
Why do you need Gerber and BOM files to provide a quote?
Gerber files provide the detailed design information needed to manufacture the PCB, including the layout of components, traces, and drill holes. The BOM (Bill of Materials) lists all the components that will be placed on the PCB. Both are essential for accurately estimating the cost of production.
Why can't you provide an accurate shipping cost before production?
The final shipping cost depends on the weight and dimensions of the finished product, which can only be determined after production. Additionally, shipping costs can vary based on factors such as the chosen shipping method, destination, and any applicable customs fees.
Why can't you determine the number of layers and cost of a PCB from a picture?
A picture of a PCB can provide some basic information, but it doesn't show the internal layers or intricate details of the design. The number of layers, materials used, and complexity of the design all impact the cost of production, and these details can only be accurately determined from the Gerber files.
How does Rowsum protect customer information and project confidentiality?
Rowsum implements strict internal controls, secure data storage and transmission, limited access policies, and collaborates only with trusted partners to ensure the confidentiality of our clients’ information and project data. We prioritize the protection of your intellectual property and business details throughout the entire process.
What sets Rowsum apart from other PCB manufacturers?
Rowsum prioritizes customer-centric solutions, cutting-edge technology, and a commitment to quality and reliability. We address common client pain points by offering competitive pricing, top-quality products, and exceptional customer support while maintaining transparency and confidentiality in our business relationships.