Introduction
Ever wondered why PTFE PCBs are the go-to choice for high-frequency applications? What sets them apart from the conventional FR4 boards in the competitive landscape of electronics?
PTFE PCBs, leveraging the unique properties of polytetrafluoroethylene, stand out for their ability to support high-frequency signals beyond 5GHz. This capability, coupled with their thermal stability, positions them as a superior choice for advanced electronic applications, earning the colloquial name “Teflon PCBs” from their association with Dupont’s Teflon brand.PTFE PCBs are predominantly used in industries where high-frequency performance is critical, such as in aerospace, telecommunications, and advanced medical devices. Their exceptional performance in these applications underscores their importance in modern electronics.
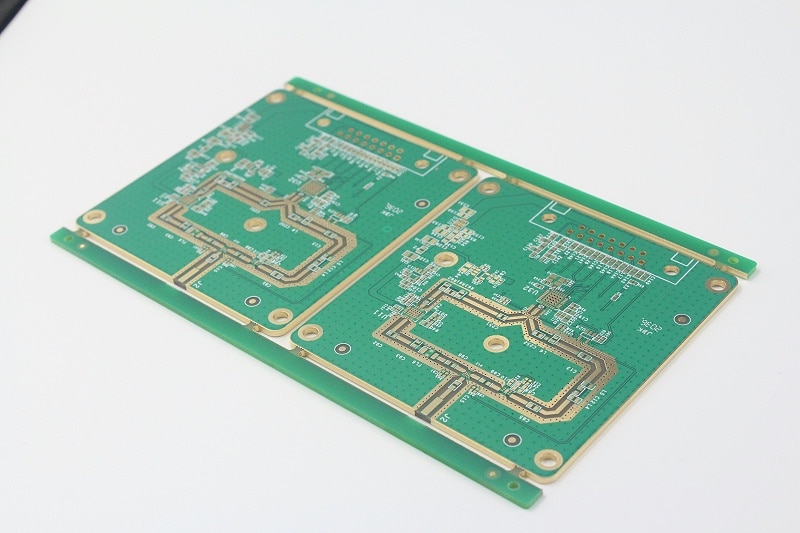
Understanding PTFE PCBs
As we delve deeper into the world of PTFE PCBs, it’s essential to appreciate the nuanced advantages and inherent challenges that come with this advanced material. The following sections will explore the multifaceted benefits that make PTFE PCBs a preferred choice for high-performance applications, as well as the practical limitations that must be considered during their design and manufacturing process. By understanding these key aspects, you’ll be better equipped to evaluate the suitability of PTFE PCBs for your specific needs and navigate the trade-offs involved in choosing them over more traditional materials like FR-4.
Advantages of PTFE PCBs
- Unmatched High-Frequency Performance: PTFE PCBs are unparalleled in their ability to support high-frequency signals, crucial for applications in advanced telecommunications and radar systems. The low dielectric constant of PTFE, typically ranging from 2.1 to 2.2, minimizes signal delay and attenuation, allowing for cleaner and faster signal transmission over a wide frequency spectrum. This is particularly significant in applications like 5G networks and aerospace communications, where the integrity of high-speed signals is paramount.
- Exceptional Thermal Stability: The thermal resistance of PTFE is extraordinary, withstanding temperatures from -200°C to +260°C. This broad temperature range ensures consistent electrical performance even under extreme conditions, making PTFE PCBs ideal for use in environments from cryogenic applications to high-temperature electronics in automotive and aerospace industries. This thermal stability not only extends the life of electronic components but also broadens the scope of their applications.
- Superior Chemical Resistance: The chemical inertness of PTFE makes these PCBs resistant to almost all chemicals, including acids, bases, and solvents. This quality is invaluable in chemical processing equipment and medical devices, where exposure to harsh sterilization chemicals or corrosive substances is common. The longevity and reliability of devices are significantly enhanced, reducing maintenance and replacement costs.
- Reliability and Durability: PTFE’s resistance to environmental stressors such as UV radiation and oxidation ensures that PCBs maintain their performance over time, even in outdoor or harsh industrial settings. This durability translates to fewer failures and longer service life, which is critical in sectors like defense and aerospace, where reliability is non-negotiable.
- Design Flexibility and Miniaturization: The flexibility in design afforded by PTFE allows for the development of complex, multi-layer PCBs that can accommodate denser circuits within smaller footprints. This capability is crucial for the ongoing trend towards miniaturization in electronics, enabling more compact and portable devices without compromising performance. Applications in wearable technology and mobile devices benefit greatly from this advantage.
- Enhanced Thermal Conductivity: While PTFE is not primarily known for its thermal conductivity, it offers sufficient heat dissipation to prevent overheating in high-speed circuitry. This aspect is particularly important in densely packed electronic assemblies where effective heat management is crucial to prevent thermal hotspots that can affect device reliability and lifespan.
Disadvantages of PTFE PCBs
- Complex Manufacturing Process: The very qualities that make PTFE advantageous also contribute to its production challenges. The material’s slippery nature, beneficial for non-stick applications, complicates the adhesion of copper layers during PCB fabrication. Manufacturers often need to incorporate additional materials like ceramics or glass fiber to enhance the mechanical stability and thermal resistance of PTFE PCBs. This not only increases the complexity of the manufacturing process but also the potential for production errors.
- Cost Implications: The specialized manufacturing requirements, along with the need for supplementary materials to bolster PTFE’s properties, contribute to higher production costs compared to standard FR4 PCBs. These increased costs can significantly impact budget considerations, particularly for projects where the high-performance attributes of PTFE are not essential.
- Thermal Expansion Concerns: Despite its excellent thermal resistance, PTFE exhibits a higher coefficient of thermal expansion compared to other PCB materials. This characteristic can lead to more pronounced dimensional changes in response to temperature variations, potentially affecting the long-term reliability of the PCB in applications subjected to fluctuating thermal environments.
- Limited Applications: The specialized nature and higher cost of PTFE PCBs often relegate their use to niche applications where their unique advantages are indispensable, such as in advanced telecommunications, aerospace, and defense technologies. This specificity limits their applicability in more general electronics projects.
- Handling and Assembly Challenges: The properties that render PTFE resistant to chemical reactions and friction also pose hurdles during PCB assembly and handling. Ensuring proper adhesion and mitigating deformation under mechanical stress require additional attention and, in some cases, specialized assembly techniques.
PTFE vs. FR-4: A Comparative Analysis
Choosing the right material for PCB manufacturing—PTFE or FR-4—depends on specific application requirements, balancing factors such as electrical performance, thermal stability, and cost. PTFE is renowned for its superior high-frequency capabilities and exceptional thermal resistance, making it ideal for demanding applications like aerospace and telecommunications. Its low dielectric constant enables faster signal transmission, critical for high-speed circuits, while its thermal endurance ensures reliability in extreme conditions.
FR-4, on the other hand, is the standard in PCB manufacturing for its versatility, mechanical strength, and cost-effectiveness. While it may not match PTFE’s high-frequency performance, FR-4’s robustness and ease of handling make it suitable for a wide range of electronics, from consumer devices to industrial systems.
Here’s a simplified table to visually compare their key properties:
Property | PTFE | FR-4 |
---|---|---|
Dielectric Constant | Low (~2.1) | Higher (4.2 – 4.8) |
Loss Tangent | Very Low (0.0002-0.0005) | Higher (0.01 – 0.025) |
Thermal Endurance | High (up to 327°C) | Moderate (130-170°C) |
Flexural Strength | Moderate (55 MPa) | High (>125 MPa) |
Chemical Resistance | Excellent | Moderate |
Cost | Higher | Lower |
This table highlights the distinct advantages and considerations of each material. PTFE stands out in environments where electrical performance and thermal resistance are paramount, but its higher cost and manufacturing complexity may not be justified for all applications. FR-4 offers a practical and cost-effective solution for a broad spectrum of PCB needs, with sufficient performance for standard applications.
PTFE PCBs in Industry Applications
Emerging Technologies and Innovations
- Space Exploration: The use of PTFE PCBs in space exploration marks a significant advancement in our quest beyond Earth. Their deployment in satellites and rovers underscores their critical role in ensuring the resilience of communication and navigation systems amidst the extreme conditions of space. The durability and reliability of PTFE PCBs under such harsh circumstances highlight their indispensability in exploring the final frontier.
- Wearable Tech: The integration of PTFE PCBs into wearable technology epitomizes the fusion of innovation and practicality. Their inherent flexibility and durability are pivotal in crafting devices that are not only compact and lightweight but also robust enough to withstand daily wear and tear, ensuring seamless performance.
Niche Applications
- High-Altitude Platforms (HAPs): PTFE PCBs are key components in HAPs, serving critical functions in atmospheric research and telecommunications. Their ability to operate effectively in low-pressure, low-temperature environments ensures the reliability of these platforms in gathering crucial data and facilitating communication from the edge of space.
- Underwater Communication Systems: The advancement of underwater communication technology heavily relies on the moisture resistance and pressure stability of PTFE PCBs. Their application in this domain ensures consistent and reliable data transmission, crucial for underwater research, navigation, and communication.
Sustainable and Green Technologies
- Renewable Energy Systems: In the realm of renewable energy, PTFE PCBs contribute significantly to the efficiency and longevity of wind turbines and solar panels. Their resistance to environmental stressors ensures that these green technologies can deliver sustainable energy solutions over extended periods.
- Electric Vehicles (EVs): The burgeoning EV market benefits from the high-frequency performance and thermal stability of PTFE PCBs, especially in critical components like power control units and battery management systems. Their reliability supports the EV industry’s growth and the transition towards cleaner transportation solutions.
Advanced Research and Development
- Quantum Computing: PTFE PCBs stand at the forefront of quantum computing research, offering potential solutions to the challenges of developing high-performance, reliable quantum circuits. Their exceptional properties may hold the key to unlocking new computing paradigms.
- Biomedical Engineering: The application of PTFE PCBs in next-generation biomedical devices underscores their importance in modern medicine. Their biocompatibility and resistance to harsh sterilization processes make them ideal for implants and sophisticated diagnostic tools, paving the way for advancements in healthcare.
This exploration into the diverse applications of PTFE PCBs across various industries not only highlights their versatility but also their critical role in driving technological progress and sustainability. As we continue to innovate and tackle global challenges, the role of PTFE PCBs in industry applications is set to expand, underscoring their importance in shaping the future of technology.
Conclusion
Throughout this exploration, we’ve unraveled the complexities and celebrated the advantages of PTFE PCBs, showcasing their pivotal role in pushing the envelope in high-frequency applications. From aerospace to the medical field, the unique properties of PTFE PCBs, such as their remarkable thermal stability and minimal dielectric losses, have been instrumental in advancing technology.
At Rowsum, we embody this spirit of innovation and precision in our approach to PCB manufacturing. Our expertise and commitment to excellence ensure that every PTFE PCB we produce meets the highest standards, aligning with the needs of industries that demand nothing short of perfection.
For those poised to harness the power of PTFE PCBs in their projects, we invite you to partner with us. Together, we can transform your visionary ideas into reality, leveraging the unparalleled capabilities of PTFE PCBs. Discover more about how we can contribute to your success by visiting us at www.rowsum.com. Let’s embark on this journey of innovation and excellence together, shaping the future of technology with every PCB we create.