Introduction
Ever wondered what keeps your electronic devices running smoothly? It’s the Power Supply Printed Circuit Board (PCB), a key component that manages power distribution in your devices. But what exactly is it, and why is it so crucial?
A Power Supply PCB is a vital part of any electronic device, converting input power into the right voltage and current for the device’s components. It ensures your devices operate efficiently and safely, preventing overheating and power surges. In essence, a well-designed Power Supply PCB is the backbone of optimal device performance.
Understanding Power Supply PCBs: A Primer
Before we delve into the intricacies of designing a power supply PCB, let’s take a moment to understand what it is and how it works. Consider this section as your primer, a brief overview to set the stage for the more detailed discussion to come. And don’t worry, we’ll be diving deeper into each aspect in the following sections.
Basic Components of Power Supply PCBs
A Power Supply PCB is made up of several key components, each playing a crucial role in its operation. These include the regulator, which controls the voltage level; capacitors and resistors, which store and regulate energy; and diodes and transistors, which control the flow of electricity. Together, these components ensure that the right amount of power is delivered to each part of your device. It’s like a well-conducted orchestra, with each instrument playing its part to create a harmonious performance.
How Power Supply PCBs Work
The primary function of a Power Supply PCB is to convert input power into the correct voltage and current for the device’s components. It does this through a process known as power conversion. The power supply takes in power from an external source, such as a wall outlet or a battery, and converts it into the voltage and current levels required by the device. This ensures that all components of the device receive the right amount of power to function optimally.
Key Considerations in Power Supply PCB Design
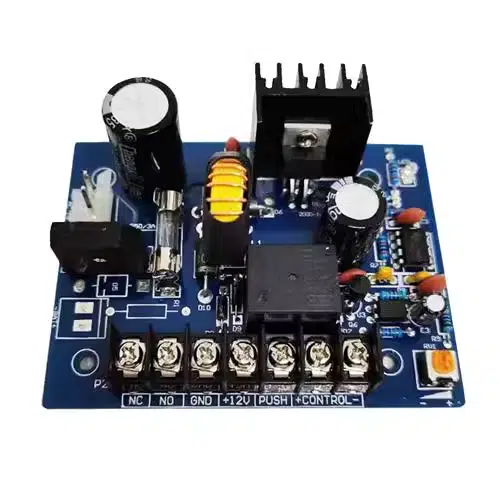
Designing a Power Supply PCB is a complex task that requires careful consideration of various factors. It’s like solving a puzzle, where each piece must fit perfectly to create the desired picture. Let’s explore these key considerations in detail:
Choosing the Right Regulator
The regulator is a critical component in your Power Supply PCB, responsible for managing the voltage supplied to the device’s components. It’s a balancing act of ensuring stability, minimizing noise, and optimizing efficiency.
In Power Supply PCB design, you’ll primarily encounter two types of regulators: Linear Regulators and Switched-Mode Regulators. Linear Regulators operate by adjusting resistance according to input voltage and load, maintaining a constant output voltage but often at the cost of efficiency. Switched-Mode Regulators, conversely, use a high-frequency switch to convert the DC input into a regulated DC output, offering higher efficiency but with increased complexity and potential for noise.
Here’s a comparison table to help you understand the differences:
Linear Regulators | Switched-Mode Regulators | |
---|---|---|
Complexity | Simple | More complex |
Output Noise | Low (noise-free output voltage) | Higher (can generate noise) |
Efficiency | Lower (can generate a lot of heat) | Higher (can handle higher input voltages) |
Use Cases | Ideal for low-power applications where noise must be minimized | Preferred for high-power applications where efficiency is a priority |
Linear Regulators
Linear regulators are simple and provide clean, noise-free output voltage. However, they are not very efficient and can generate a lot of heat. They are ideal for low-power applications where noise must be minimized. For instance, in a simple LED lighting circuit, a linear regulator could be a good choice due to its simplicity and low noise output.
Switched-Mode Regulators
Switched-mode regulators, on the other hand, are more efficient and can handle higher input voltages. However, they are more complex and can generate noise. They are preferred for high-power applications where efficiency is a priority. For example, in a laptop power supply, a switched-mode regulator would be more suitable due to its high efficiency and ability to handle higher input voltages.
Selecting the Right Components
The performance and reliability of your Power Supply PCB largely depend on the components you choose. It’s like picking the right ingredients for a recipe – the quality of the end product is determined by what you put into it.
When selecting components for your Power Supply PCB, you need to consider several factors, including their specifications, quality, compatibility with the rest of the circuit, and their suitability for your specific application.
Here are some of the key components you’ll need to consider:
Capacitors
Capacitors store and release electrical energy in your circuit. They play a crucial role in filtering noise, stabilizing voltage, and storing energy. You’ll need to choose the right type (ceramic, electrolytic, tantalum, etc.) and the right value for your specific application.
Resistors
Resistors limit current and divide voltage in your circuit. They come in various types and values, and the choice depends on your specific needs and constraints.
Diodes
Diodes allow current to flow in one direction and block it in the other. They are crucial for tasks like rectification, regulation, and signal detection.
Transistors
Transistors are used to amplify or switch electronic signals and power. They are the building blocks of modern electronic devices.
Thermal Management in PCB Design
Thermal management is a critical aspect of Power Supply PCB design. It involves strategies to dissipate heat effectively, maintain an optimal operating temperature, and prevent thermal stress on components.

Component Placement
Strategic placement of components can help manage heat distribution. High-power components, which generate more heat, should be spaced apart and placed in areas with good airflow to facilitate heat dissipation.
Heat Sinks and Thermal Vias
Heat sinks and thermal vias are essential tools for heat dissipation. Heat sinks absorb and disperse heat, while thermal vias provide a path for heat to move away from hot components to cooler areas or layers of the PCB.
Board Material
The PCB material can significantly impact heat dissipation. Materials with higher thermal conductivity, such as certain metal-core boards, can help spread and dissipate heat more effectively.
Trace Routing and Grounding
Trace routing and grounding are fundamental aspects of Power Supply PCB design. They play a crucial role in the overall performance and reliability of the power supply.
Trace Routing
Trace routing involves the paths that connect different components on the PCB. Proper trace routing is essential to ensure efficient power delivery and to minimize electromagnetic interference. It’s important to consider factors like trace width, length, and separation.
Grounding
Grounding is vital for the stability and performance of the PCB. A well-designed ground system minimizes noise and prevents interference between different circuits. It’s crucial to have a solid ground plane and to consider the placement of ground vias.
Maintaining Power Integrity
Power integrity is a crucial aspect of Power Supply PCB design. It refers to the management of power distribution from the source to the load to ensure stable and clean power to all components.
Decoupling Capacitors
Decoupling capacitors are used to maintain power integrity by filtering out noise and providing local power storage for components. They should be placed as close as possible to the power pins of the components.
Power Planes
Power planes are used to distribute power and ground signals across the PCB. They help reduce impedance, provide a return path for ground, and help with thermal management.
Voltage Regulators
Voltage regulators are used to maintain a constant output voltage. They play a crucial role in maintaining power integrity by compensating for variations in input voltage and load.
Practical Tips for Power Supply PCB Design
After understanding the key considerations in Power Supply PCB design, let’s delve into some practical tips that can help you optimize your design process:
1. Understanding the Importance of Layout
While we’ve discussed the significance of layout in the key considerations, it’s crucial to delve deeper into the practical aspects of layout planning in Power Supply PCB design.
- Optimizing Component Placement: Beyond minimizing trace lengths, consider the functional blocks of your design. Group related components together to create a logical flow of signals and power across your PCB. This not only reduces noise but also simplifies troubleshooting and maintenance.
- Leveraging Power and Ground Planes: Power and ground planes can be strategically used to shield sensitive signals from noise. Consider using a multi-layer PCB design with dedicated power and ground planes to achieve this.
- Thermal Management in Layout: Plan your layout with thermal hotspots in mind. Try to evenly distribute heat-generating components across the PCB area to prevent localized overheating. Also, consider airflow in the final product enclosure and arrange components accordingly.
2. Effective Component Placement
Component placement is more than just minimizing trace lengths. It’s about creating a functional and efficient design that meets the needs of your device. Here are some practical tips:
- Group Related Components: Place related components together to create functional blocks. This can help reduce signal delays and improve the overall performance of your PCB.
- Consider Signal Paths: Arrange components in a way that follows the natural flow of signals. This can help reduce cross-talk and electromagnetic interference.
- Manage Heat-Generating Components: Keep heat-generating components away from sensitive areas of the circuit. Also, consider the airflow in the final product enclosure and arrange components to maximize heat dissipation.
- Accessibility for Testing and Maintenance: Place components that may need to be accessed for testing or maintenance in easily accessible locations.
Remember, effective component placement can significantly improve the performance and reliability of your Power Supply PCB. Always consider the specific needs of your device and the constraints of your PCB when placing components.
3. Managing Heat Effectively
Effective heat management is crucial in Power Supply PCB design, especially when dealing with high-power components. Here are some practical tips:
- Use Thermal Vias: Thermal vias can help dissipate heat by conducting it away from heat-generating components. They can be particularly effective when used in conjunction with a ground plane that acts as a heat sink.
- Consider Component Placement: As mentioned earlier, the placement of heat-generating components can impact heat dissipation. Try to distribute these components evenly across the PCB, and consider the airflow in the final product enclosure.
- Select Appropriate Board Materials: The material of your PCB can impact its thermal performance. Materials with higher thermal conductivity can help dissipate heat more effectively.
- Design for Thermal Expansion: All materials expand when heated, and your PCB is no exception. Consider the coefficient of thermal expansion (CTE) of your PCB material and design your board to accommodate this expansion.
4. Dealing with High Currents
High currents can pose challenges in Power Supply PCB design. Here are some practical strategies for dealing with high currents:
- Use Thicker Traces: The width of your traces can impact their current carrying capacity. Thicker traces can carry more current without overheating. Use a trace width calculator to determine the appropriate width for your traces based on the current they will carry.
- Consider the Current Carrying Capacity of Your PCB: Different PCB materials have different current carrying capacities. Make sure your PCB material can handle the current levels in your design.
- Include Protection Mechanisms: Include protection mechanisms such as fuses or current limiters in your design to prevent damage due to excessive current.
- Manage Heat: High currents can generate a lot of heat. Use the heat management strategies discussed earlier to help manage the heat generated by high currents.
5. Ensuring Stability and Reliability
The stability and reliability of your Power Supply PCB are paramount. Here are some practical tips to ensure your design is stable and reliable:
- Use Decoupling Capacitors: Decoupling capacitors can help stabilize the power supply by filtering out noise and providing a reservoir of charge for the power supply. Place these capacitors as close as possible to the power pins of your ICs.
- Meet Power Requirements: Ensure that your design meets the power requirements of the device it is intended to power. This includes the voltage, current, and power quality requirements.
- Choose Reliable Components: The reliability of your PCB is only as good as the reliability of its components. Choose high-quality components from reputable manufacturers to ensure the reliability of your design.
- Ensure Quality Soldering and Assembly: Poor soldering and assembly can lead to reliability issues. Ensure that your PCB is assembled using high-quality soldering techniques and that all components are securely attached.
Understood. Here’s a revised conclusion:
Conclusion: Mastering Power Supply PCB Design
In conclusion, designing a Power Supply PCB is an intricate dance of technical decisions, each impacting the performance, reliability, and efficiency of the final product. The essence of successful Power Supply PCB design lies in the harmonious integration of components, layout, thermal management, and power integrity considerations.
However, even the most meticulously designed Power Supply PCB can fall short without the expertise of a reliable PCB manufacturer. At Rowsum, we bring your designs to life with precision, quality, and a commitment to your success.
We invite you to explore our services:
For more information or to discuss your specific needs, feel free to contact us at [email protected]. Your success is our priority.