Introduction
When choosing a surface finish for PCBs, why do many professionals gravitate towards HASL, especially when there are multiple options available? Why is HASL a distinguished choice among numerous PCB surface finishes? And how does it compare to its closest competitor, ENIG?
HASL, short for Hot Air Solder Leveling, has long been recognized in the PCB industry for its dependable performance, affordability, and versatility. In the fast-paced electronics industry, where quality and consistency are paramount, HASL offers a balance between performance and affordability. For individuals delving into the intricate world of PCB production and in search of the best surface finish, HASL frequently stands out as the preferred option.
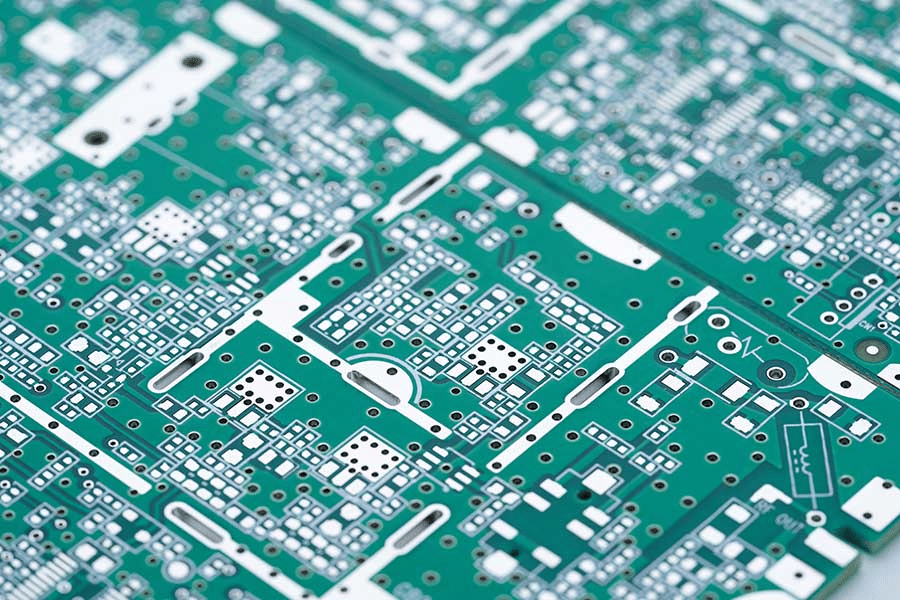
What is HASL (Hot Air Solder Leveling)?
In the realm of PCB manufacturing, Hot Air Solder Leveling (HASL) is a time-honored technique for surface finishing. Its primary function is to create a coplanar surface for the PCB, ensuring that it’s suitable for subsequent assembly processes.
How does it work?
- Pre-cleaning: The PCB undergoes a thorough cleaning to remove contaminants, residues, or oxides, ensuring optimal solder adhesion.
- Dipping in Liquid Solder: After cleaning, the PCB is dipped into a bath filled with molten solder, often a mix of tin and lead. Lead-free variants are also available in compliance with RoHS directives.
- Hot Air Leveling: A jet of hot air is applied post-immersion to remove excess solder, resulting in a uniform solder layer.
- Cooling Phase: Post immersion, the PCB undergoes cooling, enabling the solder to harden and create a uniform protective shield over the bare copper areas.
Why is it important?
- Oxidation Resistance: The solder layer prevents the underlying copper from oxidizing, preserving its solderability.
- Cost-Effectiveness: HASL is often more economical compared to other surface finishes, especially for prototypes or small batch productions.
- Visual Inspection: The bright finish allows for easy visual inspection, ensuring potential defects can be identified and rectified.
Technical Aspects of HASL
When discussing the technicalities of Hot Air Solder Leveling, it’s essential to understand the nuances that make this process both effective and preferred in many PCB manufacturing scenarios.
Composition of the Solder
Historically, the HASL procedure utilized solder made primarily from a tin-lead mixture. The most common ratio is 63% tin to 37% lead, known for its eutectic properties, meaning it has a sharp melting point. However, with the push towards environmentally friendly manufacturing due to RoHS directives, lead-free HASL variants have gained traction. Frequently, alloys like tin-copper or blends such as tin-silver-copper are employed.
Thickness Consistency
One of the primary technical challenges of the HASL process is achieving a consistent solder thickness across the PCB. The hot air knife plays a crucial role in this, ensuring that the solder is evenly spread and that any excess is removed. A uniform thickness is vital for ensuring consistent solderability during the component attachment phase.
Temperature Considerations
The molten solder’s temperature and the hot air knife are critical parameters. Typically, the solder bath temperature ranges between 255°C to 265°C for tin-lead solder and can be higher for lead-free variants. Maintaining the right temperature ensures optimal flow and adhesion of the solder to the PCB.
Substrate Interactions
The interaction between the solder and the underlying PCB substrate is a vital technical aspect. The solder must wet the copper pads effectively, ensuring a strong bond. Factors like the copper’s surface roughness, any existing oxidation, and the solder’s wetting properties all play a role in this interaction.
Limitations and Considerations
While HASL is a robust process, it’s not without its limitations. For instance, it might not be suitable for very fine-pitch components due to the potential for solder bridging. Moreover, the heat strain experienced by the PCB during HASL can pose challenges, especially for boards with sensitive components or base materials.
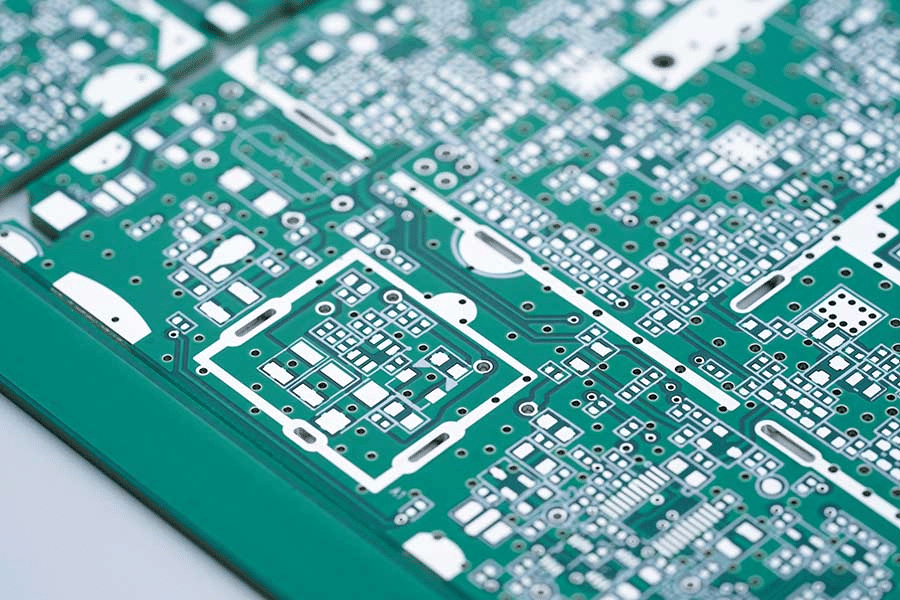
Comparing HASL with Other Surface Finishes
HASL and HASL-LF Overview
For years, Hot Air Solder Leveling (HASL) has been a favored method for PCB surface treatments. The process entails coating the PCB with liquid solder and then using hot air blades to remove any surplus. When discussing HASL, it’s essential to recognize its two distinct classifications.
- HASL: Uses a tin-lead alloy.
- HASL-LF (Lead-Free): Uses a tin-copper alloy or other lead-free combinations to comply with RoHS directives.
Aspect | HASL-LF Advantages | HASL-LF Disadvantages |
---|---|---|
Economical Aspect | Economical choice. | – |
Reliability | Reliable surface finish. | – |
Shelf Life | Long shelf life. | – |
Soldering | Suitable for both lead and lead-free soldering. | – |
Surface Flatness | – | Not the flattest surface, which can be an issue for fine-pitch components. |
Thermal Process | – | The aggressive thermal process might not be suitable for some PCBs. |
HASL-LF vs. Other Surface Finishes
HASL-LF vs. ENIG (Electroless Nickel Immersion Gold)
- Advantages of ENIG:
- Provides a flat surface, making it ideal for fine-pitch components.
- Excellent for PTH (Plated Through Hole) components.
- Extended shelf life.
- Disadvantages of ENIG:
- More expensive than HASL-LF.
- Potential for “black pad syndrome,” a type of corrosion.
HASL-LF vs. Immersion Silver
- Advantages of Immersion Silver:
- Flat surface.
- Good solderability.
- Suitable for lead-free soldering.
- Disadvantages of Immersion Silver:
- Shorter shelf life than ENIG.
- Prone to tarnishing.
HASL-LF vs. OSP (Organic Solderability Preservatives)
- Advantages of OSP:
- Environmentally friendly.
- Economical.
- Flat surface.
- Disadvantages of OSP:
- Not ideal for multiple reflow/assembly processes.
- Limited shelf life.
HASL-LF vs. Immersion Tin
- Advantages of Immersion Tin:
- Lead-free.
- Suitable for fine-pitch components.
- Disadvantages of Immersion Tin:
- Potential for whiskering over time.
- Handling sensitivity (can tarnish).
Industry Standards, Environmental, and Health Impacts
In today’s fast-paced electronics industry, choices made during the manufacturing process have implications far beyond the production line. At Rowsum, even when not explicitly specified by our clients, we’ve made a conscious decision to default to HASL-LF (Lead-Free) in our production. Why? Because we believe in prioritizing both environmental responsibility and the health and safety of our consumers.
The Environmental Toll of Traditional HASL
Traditional HASL processes, which use lead, have long-term environmental consequences. Lead contamination in soil can persist for hundreds of years, as highlighted by the United Nations Environment Programme. This not only affects ecosystems but also enters our food chain, impacting human health.
Health Implications of Lead Exposure
The Centers for Disease Control and Prevention (CDC) has emphasized the health risks associated with lead. Even minimal exposure to lead in youngsters can result in cognitive and behavioral issues, decreased intelligence quotient, and increased restlessness. In adults, it can result in fertility issues, high blood pressure, and other health complications. The repercussions of coming into contact with lead can persist throughout one’s entire life, impacting various aspects of health and well-being.
The Shift to HASL-LF: A Step Towards a Safer Future
By transitioning to HASL-LF, we’re not just adhering to industry standards like the RoHS Directive but also addressing these significant environmental and health concerns. The move to lead-free processes is not just about compliance; it’s about ensuring a safer and more sustainable future for all.
Conclusion
In the vast landscape of PCB manufacturing, the choices we make are reflections of our values. HASL-LF stands as more than just a technical choice; it embodies an industry’s commitment to quality, safety, and environmental responsibility.
Every electronic device you use has a story, a journey of decisions made to ensure its performance and longevity. At Rowsum, we’re dedicated to making choices that prioritize both the environment and the end-user.
We believe in fostering a community that values quality and sustainability. If you share our passion, we’d love to hear from you. Reach out to us at [email protected].
If you found this article helpful, please consider leaving a comment, sharing it with your network, or starting a discussion. Together, we can shape the future of electronics.
Frequently Asked Questions (FAQs)
- Is Lead-free HASL in line with RoHS standards? Absolutely. Lead-free HASL aligns with RoHS (Restriction of Hazardous Substances) guidelines. This environmentally-friendly surface finish excludes lead, making it a safer choice for electronic applications.
- What sets HASL apart in terms of benefits? HASL stands out for its cost-efficiency, reliability, and adaptability. It ensures a solder-ready surface, which is pivotal for subsequent soldering stages. Plus, HASL can help detect potential delamination issues in PCBs early on.
- Are there specific challenges associated with HASL? Indeed, while HASL is a reliable method, it has its challenges. It might not always yield a completely even surface, which can pose issues for components with fine pitches. Also, the intense thermal process might not be ideal for certain sensitive PCBs.
- How does HASL stack up against finishes like ENIG or Immersion Silver? Lead-free HASL is often more budget-friendly than ENIG. However, ENIG offers a smoother surface, ideal for fine-pitch components. Immersion Silver, on the other hand, boasts excellent solderability but might have a shorter shelf life compared to ENIG.
- What’s driving the industry’s inclination towards HASL-LF? The transition to HASL-LF, which is Lead-Free, is largely fueled by environmental considerations and standards like the RoHS directive. Lead-free HASL variants utilize materials like tin-copper alloy, which are more eco-friendly and safer for end-users.