Introduction
Ever looked at a Printed Circuit Board Assembly (PCBA) and wondered what makes it tick? What gives it its durability and consistent performance? The secret lies in a critical, yet often overlooked aspect – the surface finish.
A PCB surface finish is an intermetallic layer that serves as a bridge between the solder and the copper of the PCB. This layer is not just a protective coat against oxidation; it’s a performance enhancer, a reliability booster, and a longevity extender.
In this comprehensive guide, we will demystify the concept of PCB surface finishes. We’ll explore the various types available, their unique properties, and their applications. We’ll also delve into the crucial factors to consider when choosing the right surface finish for your needs.
Decoding the Concept of PCB Surface Finish
What is a PCB Surface Finish?
A PCB surface finish, often seen as a shiny layer on a circuit board, plays a crucial role beyond aesthetics. It’s an essential component that serves two critical functions. First, it acts as a protective shield, safeguarding the exposed copper on the PCB from oxidation and deterioration. This protective role is vital in maintaining the longevity and reliability of the PCB.
Second, the surface finish provides a solderable surface. This is crucial for the assembly process, as it allows for the secure attachment of components to the board. Without a suitable surface finish, the solder might not adhere properly, leading to potential failures in the final product.
In essence, the surface finish is a key determinant of a PCB’s performance. It influences the solderability, electrical performance, and shelf life of the board. Therefore, understanding the different types of surface finishes and their properties is crucial for anyone involved in the procurement or design of PCBs.
In the following sections, we will explore the various types of PCB surface finishes, delving into their unique properties and applications. This knowledge will empower you to make informed decisions, optimizing your procurement or design process. Let’s dive in!
Diving Deep into the Types of PCB Surface Finishes
There are several types of PCB surface finishes, each with its unique properties and applications. Here’s a quick overview:
- Hot Air Solder Leveling (HASL): A traditional surface finish that involves dipping the circuit board into a molten solder bath, providing a reliable and cost-effective finish.
- Electroless Nickel Immersion Gold (ENIG): A two-layer coating of nickel and gold, providing excellent surface planarity and suitable for fine-pitch components.
- Electroless Nickel Electroless Palladium Immersion Gold (ENEPIG): A three-layer coating of nickel, palladium, and gold, providing excellent reliability and performance for a variety of applications.
- Hard Gold: A durable surface finish that is ideal for high-wear areas, such as edge connectors.
- Immersion Silver (ImAg): A surface finish that provides good solderability and surface planarity, but requires careful handling and storage to prevent tarnishing.
- Immersion Tin (ImSn): A surface finish that provides excellent surface planarity and is suitable for fine-pitch components, but can be difficult to handle due to its sensitivity to handling and environmental conditions.
- Organic Solderability Preservative (OSP): A thin, organic coating that provides a solderable surface for copper pads, but may not be suitable for multiple reflow/assembly processes.
- Carbon Ink Surface Finish: A protective layer of carbon ink that is typically used in control panels, keypads, and other touch-control applications.
Each of these surface finishes plays a crucial role in enhancing the performance, reliability, and lifespan of a PCB. The choice of finish will depend on various factors such as the environment in which the board will be used, the applications for which they will be used, and the hours of operation.
In the following sections, we will delve deeper into each type of surface finish, discussing their specific properties, advantages, disadvantages, and ideal applications in more detail.
A Comparative Study of Different Surface Finishes
When it comes to PCB manufacturing, the choice of surface finish can significantly impact the board’s performance, cost, and suitability for specific applications. Here, we will compare several popular surface finishes, including Hot Air Solder Leveling (HASL), Electroless Nickel Immersion Gold (ENIG), Electroless Nickel Electroless Palladium Immersion Gold (ENEPIG), Immersion Silver, and Organic Solderability Preservative (OSP).
Hot Air Solder Leveling (HASL)
HASL is a tried-and-true surface finish that has been used in the PCB industry for many years. It involves coating the PCB with a layer of solder and then using hot air to level the surface. The result is a robust and solderable surface that’s ideal for conventional soldering applications. HASL is particularly popular due to its cost-effectiveness and the familiarity of manufacturers with the process.
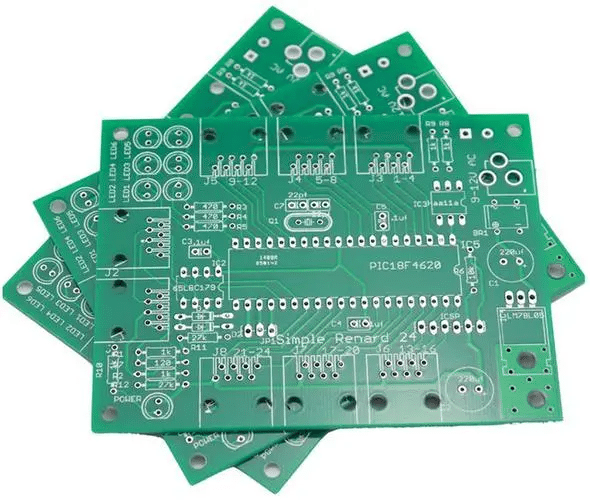
Advantages:
- Widespread Use: HASL, especially the lead-free variant (HASL-LF), is one of the most common surface finishes in the PCB industry. Its popularity stems from its long history of use and the familiarity of manufacturers with the process.
- Superior Wetting: HASL provides excellent wetting during the soldering process, ensuring a strong bond between the solder and the board.
- Protection Against Copper Corrosion: The layer of solder protects the copper from oxidation, enhancing the lifespan of the PCB.
- Large Processing Window: HASL can tolerate a wide range of temperatures and conditions during the manufacturing process, providing flexibility.
- Cost-Effective: Compared to other surface finishes, HASL is relatively inexpensive, making it a cost-effective choice for many applications.
- Good Conductivity: The solder coating used in HASL has good electrical conductivity, ensuring efficient signal transmission across the PCB.
- Good Shelf Life: The solder coating provides a protective shield, preventing the copper from oxidizing and deteriorating over time, thus extending the shelf life of the PCB.
- RoHS Compliant: HASL-LF uses only tin and its associated alloys, making it compliant with RoHS guidelines.
Disadvantages:
- Uneven Surfaces: The HASL process can lead to uneven surfaces, especially between large and small pads. This can cause issues in the assembly process, particularly for boards with fine pitch components.
- Not Suitable for Fine Pitch: HASL is not suitable for boards with less than 20mil pitch BGA and SMD, limiting its application in high-density boards.
- Thermal Shock: The high temperatures used in the HASL process can cause thermal shock to the PCB, potentially leading to damage.
Electroless Nickel Immersion Gold (ENIG)
ENIG is a two-layer surface finish that consists of an electroless nickel layer and an immersion gold layer. The nickel acts as a barrier to the copper and is solderable, while the gold protects the nickel from oxidation. ENIG is known for its excellent surface planarity, making it ideal for PCBs with fine pitch components.
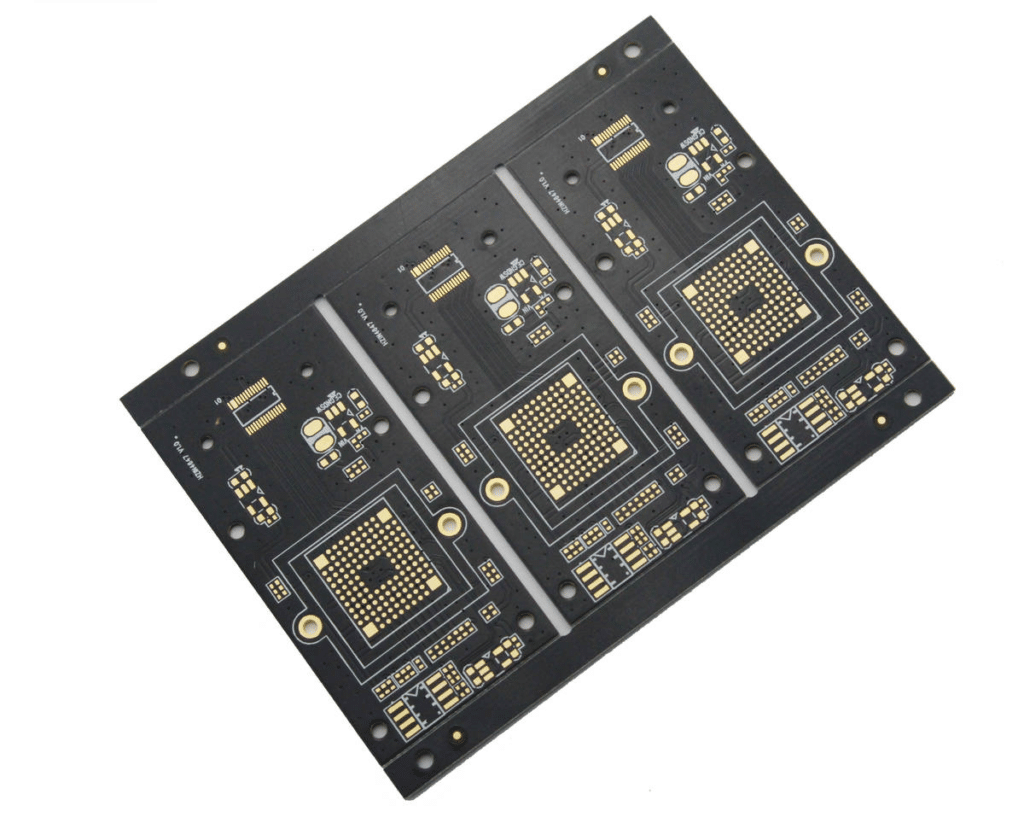
Advantages:
- Versatility: ENIG is suitable for a wide range of applications, including fine-pitch components, BGA, and flip-chip technologies. Its flat, planar surface is ideal for surface mount devices (SMDs).
- Protection: The nickel layer provides a robust barrier to copper, while the thin layer of gold protects the nickel and prevents oxidation.
- Wire Bondability: ENIG is known for its excellent solderability and wire bondability, making it a preferred choice for complex multi-layer boards.
- Long Shelf Life: ENIG offers a long shelf life, making it suitable for products with extended storage times.
- Compliance with RoHS guidelines: ENIG is lead-free and fully compliant with RoHS guidelines, making it an environmentally friendly choice.
Disadvantages:
- Cost: ENIG is more expensive than other finishes like HASL due to the use of gold and the complexity of the process.
- Intermetallic Compound Growth: Over time, the nickel layer can diffuse into the solder, leading to the growth of intermetallic compounds. This can potentially lead to brittle fractures and reduce the reliability of solder joints.
- Risk of Black Pad Syndrome: ENIG finishes are susceptible to “black pad syndrome,” a surface finish defect that can lead to poor solder joint integrity. This defect is characterized by a black or corroded appearance on the nickel surface.
Electroless Nickel Electroless Palladium Immersion Gold (ENEPIG)
ENEPIG is a multi-layered surface finish that’s becoming increasingly popular in the PCB industry. It stands out due to its unique three-layer coating structure. The first layer is electroless nickel, which provides a robust and solderable surface. The second layer is electroless palladium, which acts as a barrier to prevent the diffusion of gold into the nickel layer. The final layer is immersion gold, which protects the palladium layer from tarnishing.
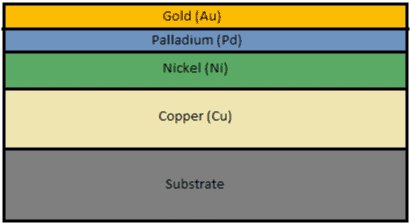
This structure provides ENEPIG with excellent reliability and performance, making it suitable for a variety of applications. It’s particularly beneficial for applications that require wire bonding, as the palladium layer provides a robust interface for both gold and aluminum wire bonding.
The key difference between ENEPIG and ENIG is the addition of the palladium layer in ENEPIG. This extra layer enhances the wire bondability of the surface finish, making ENEPIG more versatile than ENIG. However, this also makes ENEPIG more expensive and complex to apply than ENIG.
Advantages:
- Versatility: ENEPIG is a versatile surface finish that can be used for a variety of assembly techniques, including soldering connections and wire bonding with Al, Au, or Cu-wires.
- Excellent Solderability and Wire Bondability: ENEPIG finishes are characterized by their capabilities to be used as solderable and wire-bondable finish with enhanced solder joint reliability and gold-wire bondability.
- Protection Against Copper Corrosion: The layer of palladium and gold protects the copper from oxidation, enhancing the lifespan of the PCB.
- Good Shelf Life: The protective coating extends the shelf life of the PCB.
- RoHS Compliant: ENEPIG is compliant with RoHS guidelines.
Disadvantages:
- Cost: ENEPIG is more expensive than other surface finishes like HASL and ENIG.
- Complex Process: The process of applying ENEPIG is more complex than other surface finishes, requiring more steps and careful control of the process parameters.
- Potential for Running Blots: There can be running blots between patterns during the ENEPIG surface finish process, which requires careful management to prevent.
Hard Gold
Hard Gold, also known as Electrolytic Gold, is a type of surface finish applied to PCBs. It involves the application of a layer of gold over a layer of nickel. This finish is typically used in areas where repeated insertion or removal is required, such as edge connectors. The gold layer provides excellent conductivity and a high level of resistance to wear and corrosion, making it ideal for these high-stress applications.
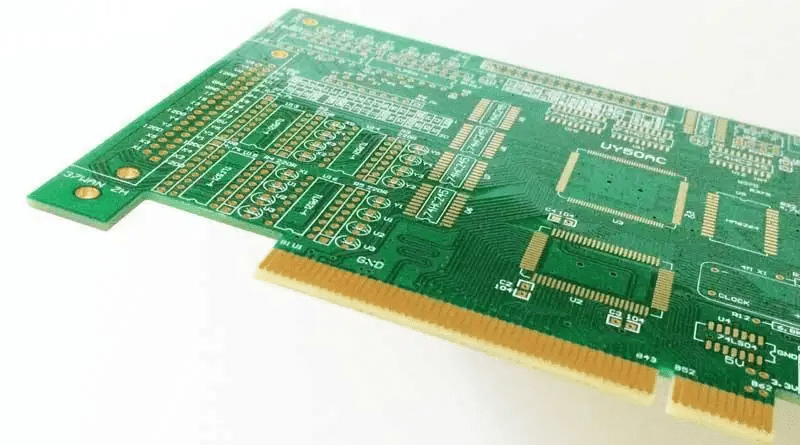
Advantages:
- Excellent Durability: Hard Gold is highly resistant to wear and tear, making it ideal for applications where repeated physical contact is expected.
- High Conductivity: The gold layer provides excellent electrical conductivity, ensuring efficient signal transmission across the PCB.
- Corrosion Resistance: Gold is highly resistant to oxidation and corrosion, enhancing the lifespan of the PCB.
- Ideal for High-Wear Applications: Hard Gold is often used on the edge connectors of PCBs due to its high level of durability and resistance to wear.
Disadvantages:
- Cost: Hard Gold is one of the most expensive surface finishes due to the cost of gold and the complex application process.
- Complex Process: The application of Hard Gold involves a complex process that requires precise control to ensure a uniform layer of gold.
- Not Suitable for Soldering: Hard Gold is not typically used for soldering due to the potential for gold embrittlement, which can weaken the solder joint.
Immersion Silver (ImAg)
Immersion Silver is a surface finish that involves depositing a thin layer of silver onto the PCB. This layer serves as a barrier, protecting the underlying copper from oxidation and enhancing the solderability of the board. Immersion Silver is known for its excellent electrical properties and is often used in high-frequency applications.
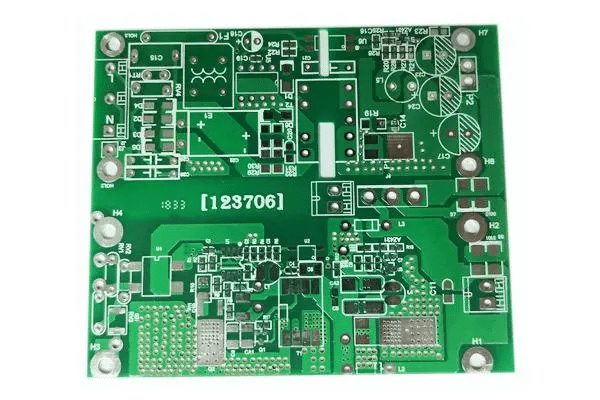
Advantages:
- Excellent Electrical Properties: Immersion Silver provides excellent electrical properties, making it suitable for high-frequency applications.
- Good Surface Planarity: This finish provides a flat surface, which is beneficial for components with a fine pitch.
- Cost-Effective: Immersion Silver is a relatively cost-effective surface finish compared to others like ENIG or ENEPIG.
- Long Shelf Life: If properly stored and handled, Immersion Silver can have a shelf life of up to 12 months.
Disadvantages:
- Silver Whiskering: Over time, silver whiskers can form on the surface of the PCB. These whiskers can cause short circuits and other reliability issues.
- Handling Sensitivity: Immersion Silver PCBs need to be handled with care to prevent tarnishing or contamination of the silver surface.
- Not Ideal for Harsh Environments: Immersion Silver is not ideal for use in harsh environments as it can tarnish easily.
Immersion Tin (ImSn)
Immersion Tin, often abbreviated as ImSn, involves depositing a thin layer of tin onto the copper layer of a PCB. This surface finish is lead-free, making it compliant with RoHS guidelines. It is an excellent choice for small geometries and components due to its ability to provide a flat surface and accommodate fine pitch components.
Advantages:
- Excellent Planarity: Immersion Tin provides a flat surface, making it suitable for fine pitch or BGA components.
- Suitable for Press-fit: The flat and smooth surface of Immersion Tin makes it ideal for press-fit applications.
- Lead-Free: Immersion Tin is a lead-free finish, aligning with environmental regulations.
- Mid-Range Cost: Compared to other surface finishes, Immersion Tin is available at a mid-range cost, making it a cost-effective choice for many applications.
- Good Solderability: Immersion Tin retains good solderability even after multiple thermal cycles.
Disadvantages:
- Handling Sensitivity: Immersion Tin finishes are sensitive to handling and can be easily damaged.
- Short Shelf-Life: Immersion Tin finishes can develop tin whiskers over time, which can lead to short circuits. This limits the shelf-life of the PCB to about 6 months.
- Unsuitable for Use with Peelable Masks: The chemical reaction between the tin and the peelable mask can lead to issues.
- Unsuitable for Contact Switches: The tin finish can wear off over time, making it unsuitable for applications that involve contact switches.
- Special Equipment Setup Required: Immersion Tin finishes require a special setup for electrical testing, such as soft probe landing.
Organic Solderability Preservative (OSP)
OSP, or Organic Solderability Preservative, is a unique surface finish that provides a very thin protective layer over the bare copper of a PCB. Unlike other finishes that use metals like gold, silver, or tin, OSP utilizes an organic compound to protect the copper from oxidation. This organic layer is water-based, making OSP an environmentally friendly option. It’s a popular choice for its simplicity and cost-effectiveness, but it’s not without its limitations, which we’ll explore below.
Advantages:
- Cost-Effective: OSP is one of the least expensive surface finishes, making it a popular choice for cost-sensitive applications.
- Flat Surface: OSP provides a very flat surface, which is beneficial for PCBs with fine pitch components.
- Simple Process: The process of applying OSP is relatively simple compared to other surface finishes, making it less time-consuming and more efficient.
- Lead-Free and RoHS Compliant: OSP is a lead-free finish, making it compliant with RoHS guidelines.
Disadvantages:
- Limited Shelf Life: OSP has a shorter shelf life compared to other finishes. The organic layer can deteriorate over time, reducing the solderability of the PCB.
- Handling Sensitivity: OSP finishes are sensitive to handling and can be easily damaged. This requires careful handling during the assembly process.
- Not Suitable for Multiple Reflow/Assembly Processes: OSP is not ideal for PCBs that require multiple reflow or assembly processes, as the organic layer can degrade with each cycle.
I understand your point. I apologize for any confusion. Let’s revise the Carbon Ink Surface Finish section with more detail and context:
Carbon Ink Surface Finish
Carbon Ink Surface Finish is a unique type of surface finish that involves the application of a conductive carbon ink over specific areas of the PCB. This finish is typically used in applications where a non-metallic conductive layer is required, such as in keypads, keyboards, and remote controllers. The carbon ink provides a conductive path for these applications, enabling the functionality of the buttons or keys.
Unlike other surface finishes that cover the entire PCB, Carbon Ink Surface Finish is applied only to specific areas that require conductivity. This selective application makes it a versatile choice for PCBs that need to integrate with rubber or silicone keypads. The carbon ink forms a conductive bridge between the keypad and the circuit, enabling the transfer of signals when a key is pressed.
Advantages:
- Selective Application: Carbon Ink Surface Finish can be applied to specific areas of the PCB, providing flexibility in its use.
- Conductive: The carbon ink provides a conductive path, making it ideal for applications like keypads and remote controllers.
- Cost-Effective: Compared to other finishes like hard gold, Carbon Ink Surface Finish is a more cost-effective solution for achieving conductivity in specific areas.
Disadvantages:
- Limited Use: Carbon Ink Surface Finish is not suitable for all types of PCBs. It’s primarily used for specific applications and may not be the best choice for PCBs that require a uniform finish across the entire board.
- Handling Care: PCBs with a Carbon Ink Surface Finish require careful handling to avoid damaging the carbon ink layer.
Surface Finish | Cost | Conductivity | Durability | Complexity | Shelf Life | Solderability | Unique Features |
---|---|---|---|---|---|---|---|
HASL | Low | Good | Good | Low | Good | Excellent | Widespread use, good for conventional soldering |
ENIG | High | Excellent | Excellent | Medium | Excellent | Excellent | Ideal for fine pitch components, wire bondability |
ENEPIG | High | Excellent | Excellent | High | Excellent | Excellent | Versatile, excellent for soldering and wire bonding |
Hard Gold | High | Excellent | Excellent | High | Good | Fair | Ideal for high-wear applications, excellent durability |
Immersion Silver | Medium | Excellent | Medium | Medium | Good | Excellent | Good for high-frequency applications |
Immersion Tin | Medium | Good | Good | Medium | Fair | Excellent | Suitable for press-fit applications |
OSP | Low | Good | Fair | Low | Fair | Good | Environmentally friendly, simple process |
Making the Right Choice: Selecting the Appropriate PCB Surface Finish
Choosing the right surface finish for your PCB is a critical decision that can impact the performance, reliability, and cost of your product. Here’s a step-by-step guide to help you make an informed decision:
- Start with HASL-LF: Hot Air Solder Leveling (Lead-Free) is a cost-effective and widely used surface finish that provides a robust and solderable surface. It’s suitable for conventional soldering applications and can tolerate a wide range of temperatures and conditions during the manufacturing process. However, it’s not suitable for boards with less than 20mil pitch BGA and SMD due to the risk of uneven surfaces. This makes it a good choice for general electronics and low-density boards.
- Consider ENIG for finer pitch components: If your PCB design includes fine pitch components (less than 20mil pitch), Electroless Nickel Immersion Gold (ENIG) may be a better choice. It offers excellent surface planarity, making it ideal for surface mount devices (SMDs) and Ball Grid Array (BGA) components. However, it’s more expensive than HASL-LF and there’s a risk of black pad syndrome, a surface finish defect that can lead to poor solder joint integrity. ENIG is often used in high-density and high-frequency applications like telecommunications and networking devices.
- Look to ENEPIG for wire bonding applications: If your application requires wire bonding, particularly with gold or aluminum wires, Electroless Nickel Electroless Palladium Immersion Gold (ENEPIG) could be the best option. It provides a robust interface for both gold and aluminum wire bonding. However, it’s more expensive and complex to apply than ENIG. ENEPIG is typically used in high-reliability applications such as aerospace and medical devices.
- Consider other finishes for specific needs: If your application has specific requirements that aren’t met by HASL-LF, ENIG, or ENEPIG, there are other finishes to consider. For example, Hard Gold is ideal for high-wear applications such as edge connectors due to its high level of durability and resistance to wear. Immersion Silver is suitable for high-frequency applications due to its excellent electrical properties. Immersion Tin is a cost-effective, lead-free finish that’s suitable for fine pitch or BGA components, but it has a short shelf-life and is sensitive to handling.
Conclusion
Selecting the right PCB surface finish is a balance between performance, reliability, and cost. While HASL-LF is a cost-effective solution for many applications, more demanding scenarios may require advanced finishes like ENIG or ENEPIG. The key is understanding your product’s specific needs and aligning them with the right surface finish.
Always remember, the best surface finish is the one that ensures optimal performance throughout the product’s lifespan, within your budget and manufacturing constraints. Make an informed decision, and you’re on your way to a successful product.