Introducción
¿Qué factores influyen en la selección de colores para los PCB y qué papel desempeñan estos colores en su funcionalidad y diseño? En el mundo de la electrónica, el color de una placa de circuito impreso (PCB) va mucho más allá del mero valor estético; es parte integral de la funcionalidad de la placa.
La familiar capa verde que se ve encima de la mayoría de los PCB se conoce como máscara para soldar. Esta capa es fundamental para definir el color de la PCB y juega un papel clave en la funcionalidad de la placa. Actúa como aislante de las trazas de cobre del circuito, evitando cortocircuitos y protegiendo contra daños ambientales. La elección del verde como color estándar se debe a su capacidad para equilibrar el costo, la capacidad de fabricación y la facilidad de inspección. Este color ofrece un excelente contraste, ayudando en la detección de fallas. Por el contrario, los PCB negros se utilizan comúnmente en aplicaciones donde la disipación de calor es crítica y los PCB blancos se prefieren en Aplicaciones LED para mejorar la reflexión de la luz y la eficiencia.
El papel, la composición y la historia de la tinta PCB verde
La máscara de soldadura verde, ahora un elemento básico en el diseño de PCB, tiene una historia arraigada en la evolución de la fabricación de productos electrónicos. Esta distintiva capa verde, más que una simple elección de color, es un componente crítico de la funcionalidad de la PCB. Conocida técnicamente como máscara de soldadura, está hecha de un polímero especializado, generalmente una resina epoxi mezclada con pigmento verde. Esta formulación sirve para proteger los circuitos de cobre del aire, la humedad y posibles cortocircuitos, al mismo tiempo que proporciona una superficie duradera y soldable.
En los primeros días de la fabricación de PCB, después de la Segunda Guerra Mundial, la industria enfrentó desafíos con trazas de cobre desprotegidas. Estos rastros eran susceptibles a la corrosión y daños, lo que provocaba frecuentes fallos. La introducción de máscaras de soldadura a finales de los años 1950 y 1960 marcó un avance significativo. Sin embargo, estas aplicaciones iniciales eran básicas y carecían de la precisión de las técnicas modernas.
La elección del verde se debió inicialmente a la disponibilidad y compatibilidad del material. Los pigmentos verdes estuvieron entre los primeros compatibles con las resinas epoxi utilizadas en las máscaras de soldadura. Este color ofrecía un excelente contraste con los rastros de cobre y las marcas de serigrafía típicamente blancas, lo que facilitaba a los técnicos la inspección e identificación de cualquier problema. Además, el tono verde cansaba menos la vista, un factor importante para los técnicos que trabajaban con PCB durante períodos prolongados.
A medida que avanzó la tecnología de fabricación de PCB, la máscara de soldadura verde se convirtió en el estándar de la industria. Esta estandarización fue impulsada por la capacidad de la máscara verde para equilibrar el costo, la capacidad de fabricación y la facilidad de inspección. La adopción generalizada de máscaras de soldadura verdes condujo a optimizaciones en el proceso de aplicación, convirtiéndolas en una opción confiable y económicamente viable para los fabricantes de PCB.
Hoy en día, la máscara de soldadura verde es emblemática de la historia y el progreso tecnológico de la industria de PCB. Si bien los avances modernos han introducido una variedad de colores de máscaras de soldadura, el verde sigue siendo un testimonio de los primeros días de innovación y estandarización de la industria. Simboliza el equilibrio entre funcionalidad, rentabilidady capacidad de fabricación que es esencial en el diseño de PCB.
Implicaciones funcionales de las variaciones de color en el diseño de PCB
PCB verdes:
- Ventajas:
- Gestión Térmica: Fiable para la gestión del calor: las máscaras de soldadura verdes son conocidas por su eficaz resistencia al calor, lo que las hace adecuadas para diversas aplicaciones.
- Producción optimizada: Su uso común en la industria ha llevado a que los procesos de fabricación se ajusten con precisión para obtener PCB ecológicos, lo que mejora la eficiencia de la producción.
- Desventajas:
- Uniformidad estética: Pueden carecer de carácter distintivo en productos donde el diseño único es un factor clave.
- Uso típico: Dominante en una amplia gama de dispositivos electrónicos, particularmente donde es esencial equilibrar el costo y el rendimiento confiable.
PCB azules:
- Ventajas:
- Diferenciación estética: Ofrece una alternativa visualmente distinta, adecuada para productos de consumo donde la apariencia es un factor.
- Resistencia al calor moderada: Generalmente proporciona un equilibrio entre visibilidad y rendimiento térmico.
- Desventajas:
- Facilidad de inspección variable: En determinadas condiciones de iluminación, es posible que el contraste no sea tan eficaz como el de las PCB verdes para la detección de fallos.
- Uso típico: Los PCB azules se utilizan a menudo en kits educativos y electrónicos para aficionados, como ciertos modelos de Arduino, donde el atractivo visual es importante.
PCB rojos:
- Ventajas:
- Alta visibilidad para componentes: Buen contraste para la colocación de componentes, lo que puede resultar beneficioso en diseños complejos.
- Apariencia distintiva: Ofrece una apariencia audaz y única para productos orientados al consumidor.
- Desventajas:
- Absorción de calor: Puede absorber más calor, lo que podría afectar a los componentes en entornos de alta temperatura.
- Uso típico: Los PCB rojos se encuentran comúnmente en hardware de juegos y computación de alto rendimiento, donde tanto la estética como la visibilidad de los componentes son importantes.
PCB negros:
- Ventajas:
- Estética: Proporciona una apariencia elegante y premium, ideal para dispositivos electrónicos de alta gama.
- Disipación de calor: Bueno para aplicaciones con cargas térmicas más altas debido a una mejor absorción de calor.
- Desventajas:
- Desafíos de inspección y reparación: Un contraste inferior con las pistas y las almohadillas puede dificultar la identificación de defectos.
- Uso típico: Los PCB negros se utilizan normalmente en productos electrónicos de consumo avanzados, como teléfonos inteligentes y sistemas de sonido de lujo, donde el diseño y la gestión del calor son fundamentales.
PCB blancos:
- Ventajas:
- Reflectividad: Excelente para aplicaciones LED ya que mejora la eficiencia de la luz.
- Aspecto moderno: Adecuado para dispositivos donde la PCB es parte del atractivo estético.
- Desventajas:
- Mantenimiento: Más propenso a manchas visibles y requiere un manejo cuidadoso durante el montaje.
- Uso típico: Se utiliza habitualmente en soluciones de iluminación LED y electrónica decorativa donde la PCB contribuye al diseño general y a la eficacia de la luz.
PCB amarillos:
- Ventajas:
- Alta visibilidad y contraste: Las máscaras de soldadura amarillas ofrecen una visibilidad excelente, con un alto contraste entre la máscara de soldadura y los rastros de cobre. Esta característica los hace adecuados para PCB que requieren una inspección detallada.
- Estéticamente agradable: Proporciona una apariencia brillante y distintiva, lo que puede resultar ventajoso para productos orientados al consumidor donde el atractivo visual es un factor.
- Desventajas:
- Visibilidad de la serigrafía: Los PCB amarillos pueden presentar desafíos en la legibilidad de la serigrafía, especialmente si se utiliza tinta blanca tradicional.
- Uso típico: Los PCB amarillos se emplean a menudo en electrónica especializada donde la diferenciación visual es importante, como en ciertos kits educativos o experimentales.
PCB morados:
- Ventajas:
- Atractivo estético único: Ofrece una apariencia única y vibrante, diferenciándolos de los colores más tradicionales.
- Buen contraste con la serigrafía: Proporciona un contraste razonable para el etiquetado de componentes y la visibilidad del seguimiento.
- Desventajas:
- Costo y disponibilidad: A menudo son más caros y menos disponibles que otros colores debido a sus requisitos únicos de pigmento.
- Uso típico: Los PCB morados se utilizan a veces en productos electrónicos personalizados o especializados, como productos electrónicos de bricolaje o fabricación a pequeña escala, donde se desea una identidad visual distintiva.
Color | Ventajas clave | Desventajas notables | Uso común en productos |
---|---|---|---|
Verde | Lo mejor para inspecciones, estándar de la industria | Demasiado común para aplicaciones únicas | Electrónica de consumo como televisores, computadoras, electrodomésticos. |
Azul | Llamativo atractivo visual, buena gestión del calor. | Menor visibilidad de inspección que el verde | Proyectos de electrónica de bricolaje, kits de robótica educativa. |
Rojo | Aspecto vivo, diferenciación de componentes. | Mayor absorción de calor | Consolas de juegos, tarjetas gráficas de alta gama. |
Negro | Estética elegante, absorción de calor mejorada | Difícil de inspeccionar | Equipos de audio premium, smartphones avanzados |
Blanco | Reflectante (ideal para LED), apariencia moderna | Mayor mantenimiento, riesgo de decoloración. | Tiras de luz LED, dispositivos domésticos inteligentes modernos |
Amarillo | Excelente visibilidad y contraste, llamativo. | Problemas de legibilidad de la serigrafía | Equipos de prueba especializados, placas prototipo. |
Púrpura | Único y distintivo para la marca. | Mayores costos de producción, menor disponibilidad. | Dispositivos IoT personalizados, electrónica de consumo de edición limitada |
Selección de colores según las necesidades del proyecto: adaptación de su elección a la aplicación
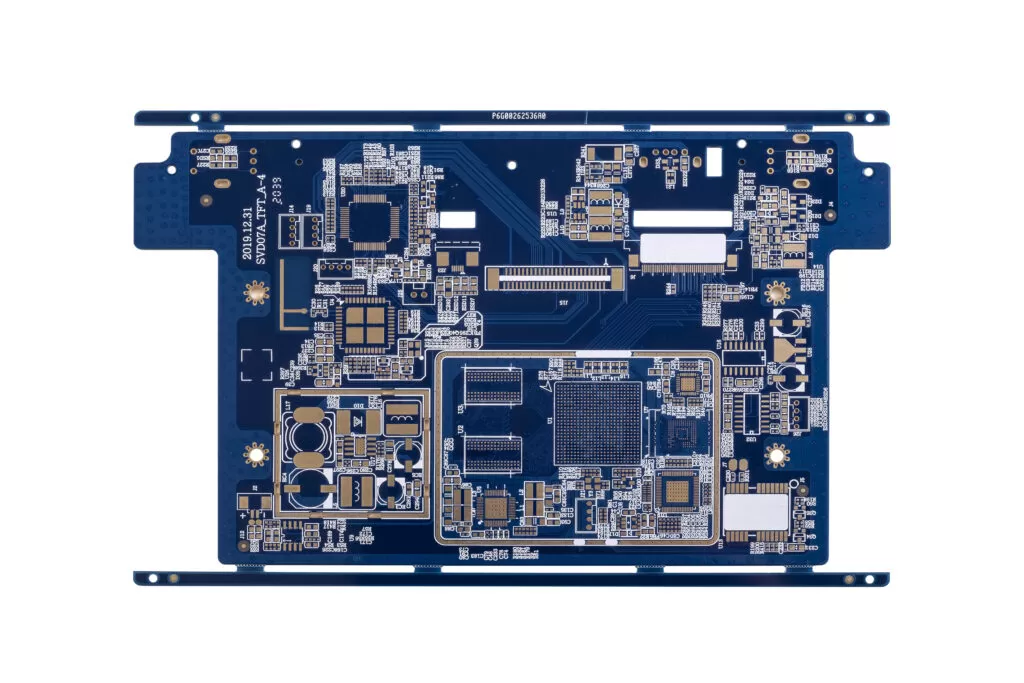
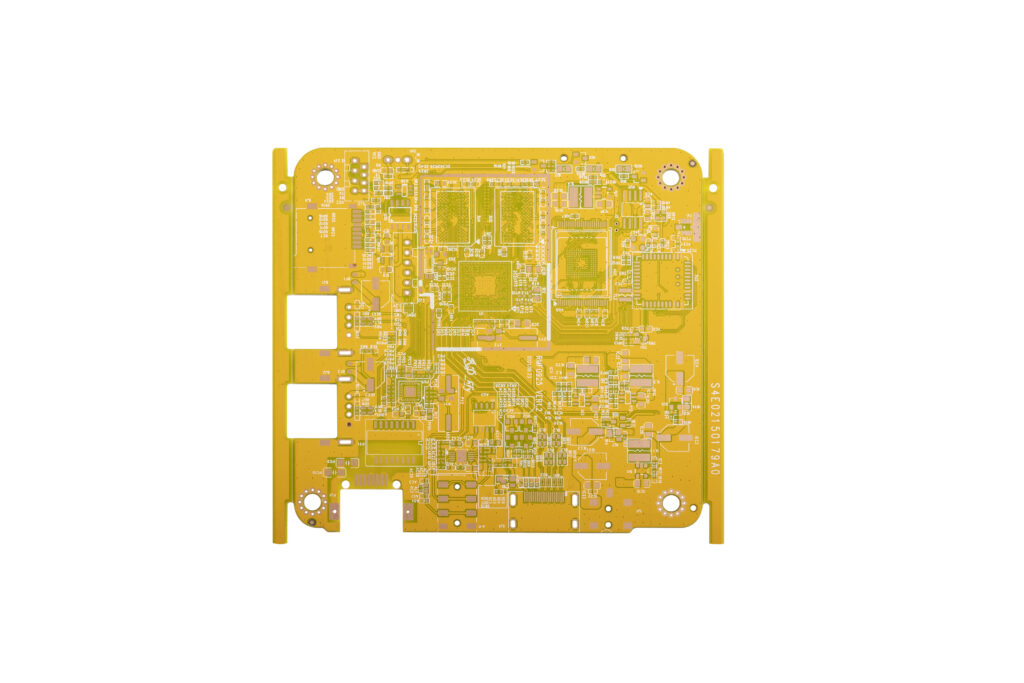
Cuando se trata de elegir el color de máscara de soldadura adecuado para su PCB, es esencial considerar las necesidades específicas de su aplicación. Esta decisión debe equilibrar los requisitos funcionales, el costo y la estética. Aquí hay una guía adaptada a varios tipos de PCB:
Evalúe las necesidades específicas de la aplicación:
- PCB LED: Opte por máscaras de soldadura blancas debido a su excelente reflectividad, que mejora la eficiencia y el brillo de los LED.
- Electrónica de alto rendimiento: El negro es ideal cuando la disipación de calor es fundamental, ya que absorbe el calor de forma eficaz.
- Electrónica de consumo: Para productos donde la PCB es visible, como ciertos dispositivos, los colores vibrantes como el azul y el rojo pueden alinearse con el diseño estético del producto.
- Industrial y Automotriz: El verde es una opción sólida por su durabilidad y rentabilidad, mientras que el negro se puede elegir por su resistencia al calor.
- Dispositivos médicos: Las máscaras de soldadura verdes y amarillas brindan la visibilidad y el contraste necesarios para inspecciones y diseños complejos, esenciales en aplicaciones médicas.
Considere los costos y la eficiencia de fabricación:
- Verde: Ofrece beneficios económicos debido a su uso generalizado, lo que conduce a procesos de fabricación optimizados y rentables.
- Otros (Amarillo, Rojo, Morado): Estos colores pueden implicar mayores costos y potencialmente una menor eficiencia de producción debido a una menor estandarización.
Necesidades de visibilidad e inspección:
- Alto contraste: El verde y el amarillo son excelentes para inspecciones detalladas y diseños de circuitos complejos, ya que brindan una visibilidad superior.
- Sistemas de inspección automatizados: Los sistemas a menudo optimizados para PCB verdes pueden ser más eficientes debido al alto contraste del color y la familiaridad en la industria.
Estética y marca:
- Identidad de marca única: Si la PCB contribuye al atractivo visual del producto, seleccionar un color único como azul, rojo o morado puede mejorar el diseño general y alinearse con la identidad de la marca.
Guía de decisión rápida:
- Electrónica estándar y general: El verde es la opción preferida por su equilibrio entre costo, eficiencia y funcionalidad.
- Productos LED y centrados en la luz: El blanco mejora el reflejo de la luz, lo que lo convierte en la opción preferida.
- Electrónica de consumo de alta gama: El negro ofrece una apariencia premium y es adecuado para productos que requieren una gestión eficiente del calor.
- Electrónica especializada: Se puede seleccionar amarillo o morado por su apariencia distintiva y necesidades de diseño específicas.
Al considerar cuidadosamente estos factores, puede seleccionar un color de máscara de soldadura para PCB que no solo cumpla con los requisitos técnicos de su proyecto, sino que también se alinee con los objetivos de diseño y marca de su producto. La elección definitiva debe complementar los objetivos de su proyecto, ya sea rentabilidad, optimización del rendimiento o estética del diseño.
Conclusión
Como hemos visto, la elección del color de la máscara de soldadura de PCB es más que una preferencia cosmética; es una decisión estratégica que influye en la funcionalidad, la facilidad de inspección y la estética del producto.
En Rowsum, entendemos la importancia de estas elecciones. Es por eso que ofrecemos una gama de colores de PCB para satisfacer las necesidades específicas de su proyecto: verde, blanco, negro, rojo, amarillo, morado y azul. Ya sea que esté buscando la practicidad del verde, la reflectividad del blanco para sus proyectos LED, la sofisticación del negro o la vitalidad de otros colores, tenemos la capacidad de darle vida a su diseño con precisión y calidad.